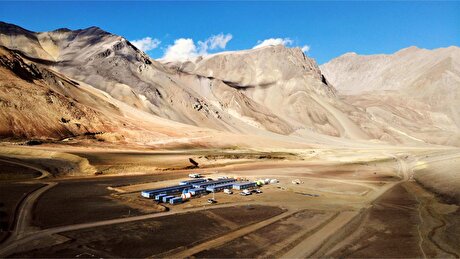
Relying on the institutionalized experience and expertise of the experts and specialist staff of the Refractory Repair Center and the Steelmaking and Continuous Casting Unit, the use of modern knowledge and the continuous improvement of the quality of refractory materials produced in the country, provided conditions that the life of shell refractory and duct block of electric arc furnaces And Patil molten slag line should be increased to the highest possible level and finally, the amount of refractory consumption in the entire steel industry, by recording a record of 5.74 kg of molten barrels in October, will be the lowest amount of refractory consumption in the history of Mobarakeh Steel.
The recently registered refractory life records are: Patil slag line life from 63 to 82 melting, electric arc furnace loose refractory life from 400 to 612 melting, and electric arc furnace life (without piping) from 160 to 175 melting.
After achieving this success, a group of leaders and experts in this field said the following about how to achieve this record:
Reza Jahanshahi, the head of the refractory technical group of Mobarakeh steel, stated: Since the beginning of Mobarakeh steel, the refractory repair center tried to provide maximum support to the production lines, to carry out periodic inspections and repairs of the refractory equipment with the best possible quality, and the downtime due to repairs Reduce fire to a minimum.
He added: One of the indicators of fireproofing performance in this area is the life of fireproofing equipment, which is evidenced by recent records in reducing costs and increasing the fireproofing life of equipment.
Jahanshahi pointed out: 95% of Mobarakeh Steel's refractory material consumption is related to the company's steelmaking area. Considering the importance of competitive and economic production in today's world, managing the refractory share of the conversion cost and the finished price of Takthal is one of the main goals of the Refractory Repair Center. Research plans and implementation of projects to increase the quality of consumable refractory materials in accordance with production conditions, improve the quality of fireproofing, continuous and effective inspection of fireproofing equipment and interaction with operating units to control the parameters affecting the use and efficiency of fireproofing.
The head of the Refractory Technical Group of Mobarakeh Steel stated: The achievement of these records is the result of the efforts, empathy and brilliant performance of all the company's colleagues, especially the tireless efforts of the Refractory Repair Center and the continuous steelmaking and casting area, the cooperation of the purchasing units of consumables and material control, the contractors in the area and The hard work of the refractory production companies, for which we sincerely appreciate them.
Ahmedreza Iranpour, the head of refractory repairs at Fould Mobarakeh steel plant, said: In line with the goals of the organization, increasing productivity, reducing costs and increasing production, the amount of refractory material consumption in steelmaking and continuous casting is one of the important and influential factors.
He added: Considering that increasing the fireproof life of equipment is directly related to reducing downtimes, reducing costs and increasing production, in order to reduce the amount of fireproof materials in the three axes of quality of consumables, implementation of high-quality fireproofing and proper operation, several projects were carried out.
Yaranpour stated: In order to provide suitable and high-quality materials, several meetings were held with suppliers. During these meetings, we focused on the chemical analysis of various materials until the proper quality of the used material was established.
In addition, for the purpose of high-quality fireproofing, the revision of instructions, training of employees and the use of new fireproofing methods were put on the agenda, and in order to properly use the equipment, a very coherent cooperation was carried out by the colleagues of the operation department in such a way that the best operating conditions and the achievement of a record of 82 smelters The refractory life of Patil slag line and the record life of duct blocks of arc furnaces were 175 melting and 612 shell melting, which deserves to be appreciated by our hardworking colleagues in operation and refractory repair center and all refractory manufacturing companies.
Ali Nouri, an expert of Mobarakeh Fould's Refractory Technical Group, stated: The record of 82 meltings in the slag line of Mobarakeh Fould's melting pots happened while the previous record of refractory life in this line was 63 meltings in 1401, which is an increase in life with a jump of about 30 There is a percentage that is unique in its kind.
He added: In addition to reducing the significant cost, increasing the life of the refractory is also effective in the standby of the equipment. In general, reducing the consumption of magnesia refractories, reducing the frequency of replacing the Patil slag line, reducing gas and energy consumption, reducing the man-hour cost of power, and reducing refractory waste are other important benefits of obtaining this record.
Nouri explained: Among the other factors that had an impact on achieving this record, we can improve the quality of refractory materials, reduce potyl stops, reduce LF and POT times, increase accuracy in continuous potyl inspections, necessary research and follow-up on the quality of produced refractory materials and improvement projects. Cited. He continued: This record in the production conditions of Mobarakeh Steel, which has LF and RH units in continuous casting, is exceptional and is considered a long life compared to similar companies. We will achieve 100 melting in Patilas slag line.
Alireza Naderi, an expert in refractory repairs at Mobarakeh Steel Factory, said: Meanwhile, we achieved the record of the shell refractory life of arch furnaces at the rate of 612 melts, while the previous average life was around 400 melts. By holding expert meetings and identifying the necessary measures to increase the life of fireproofing to increase the amount of production along with reducing stoppages, it was investigated. Identification of areas of arc furnace refractories that are more exposed to corrosion in the production process was done with the cooperation of a very good team of production and repair units of electric arc furnaces, refractories repair center and technical offices.
Also, by holding meetings with the R&D unit of Mehrgadaz Company, which is the supplier of refractories for arc furnaces, the refractories center unit considered measures such as changing the quality of bricks in areas sensitive to corrosion and ordering bricks with special dimensions for areas exposed to more corrosion. In the end, we appreciate the assistance and support of the management of Neszuz center, district management, production management, as well as the colleagues of production units, repairs, technical offices, Neszuz center and Mehrgadaz company.
Sadegh Ranjbar, an expert in Patil Foulad Mobarakeh service, said: In line with the goal of reducing costs in Mobarakeh Foolad Company and in the light of God's grace and relying on the expertise and skill of the staff of the Refractory Repair Center, the records of 73 and 82 melts in the life of the Patil slag line were melted in October 1402. was achieved He added: The staff of Mobarakeh Refractory Repair Center with the cooperation of the employees of the continuous steelmaking and casting area achieved the above valuable records by performing a series of activities.
Some other measures that were effective in obtaining this record are: managing the number of vats in the cycle, reducing the empty time of the molten vat, charging the optimal amount of lime in arc furnaces and secondary metallurgy, the number of vats in the cycle, reducing the empty time of the molten vat, Charging the optimal amount of lime in arc furnaces and secondary metallurgy.