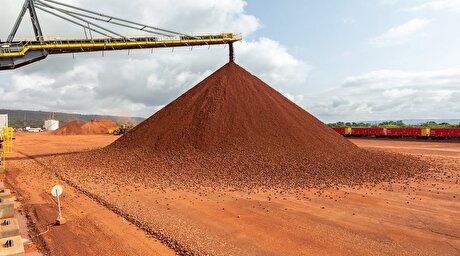
IISCO Steel Plant, a SAIL group company, India, and SMS group have successfully commissioned an X-Melt® converter shop for the production of quality steel grades at the Burnpur location in the Indian federal state of West Bengal.
The new steelworks is rated for an annual production of 2.6 million tons of liquid steel. The steelworks comprises three converters each with a tapping weight of 150 tons, three stirring stations, two ladle furnaces, an RH-TOP vacuum circulation degassing plant, primary and secondary gas cleaning systems and a converter off-gas recovery system.
The SMS group scope of supply comprised the complete basic and detailed engineering of the mechanical core components and the complete X-Pact®electrical and automation systems. Delivery, erection, commissioning, commissioning supervision as well as training of the operating personnel were also part of the contract.
The BOF converters are equipped with the maintenance-free lamella suspension system developed by SMS group, with bottom-stirring systems for combined blowing and with the tilt drive systems manufactured in SMS group’s own workshop in Hilchenbach, Germany.
The supply scope further includes the oxygen blowing lance system, the additives handling system, ladle lining repair facilities and the railbound ladle transfer vehicles.
X-Melt® Converter steel plant from SMS group
The RH-TOP vacuum degasser is of a rocker-type design, using a hydraulic counterweight system for lowering the vessel into the ladle for treatment. The unit features an SMS Mevac multifunction TOP lance combining oxygen blowing and an oxygen fuel burner for vessel heating. The degasser is complete with an extensive alloy addition system. The scope of supply for SMS Mevac comprised all the technological equipment, including the vacuum pump and TOP lance system, and the complete supply of the first fill of the main refractory materials.
For primary gas collection, use is made of the proven SMS group adjustable skirts for the recovery of the energy-containing CO gas. SMS group also supplied the off-gas cooling system, the wet-type scrubbers, the gas change-over and export stations, and a gas tank with a volumetric capacity of 50,000 Nm³ converter off-gas. With the aid of this technology, every year a volume of 200 million Nm³ converter off-gas can be used to replace other fossil fuels for energy production. Not only the energy costs but also the output of CO2can thus be considerably reduced.
Secondary gas cleaning is performed by means of easy-to-maintain electrostatic precipitators (ESP), rated for a capacity of more than 1,870,000 Nm³ per hour.
The X-Pact® electrical and automation system has been specifically adapted to the mechanical components of the plant and, in addition to the technological control systems (level 1), it includes the metallurgical process models (level 2), ensuring economical production and a high steel quality.