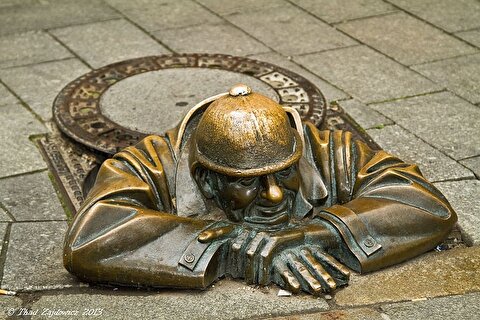
Iron ore is an important raw material for iron and steel production enterprises. After processing, we can get iron from natural minerals (iron ore), which is the mineral aggregates that contain iron or iron compounds and can be used economically.
Iron exists in nature in the form of compounds, especially in the form of iron oxide. There are many types of iron ore, for instance, the Magnetite (Fe3O4) and Hematite (Fe2O3 and FeCO3) are mainly two kinds of iron ore that used for iron making.
Generally, the processing of iron ore needs several stages, including crushing, grinding, ore beneficiation, concentrating, drying, etc. The equipment for iron ore beneficiation consists of Jaw Crusher, Ball Mill,Classifier, Magnetic Separator, Flotation Machine, Concentrator Machine, and Dryer, and Equipped with Feeder, Elevator, and Conveyor, etc.
According to different extent form, classification of iron ore have hematite, limonite, magnetite, siderite, etc. According to different iron ore types, iron ore beneficiation processes mainly refer to magnetic separation, flotation separation, gravity separation, and magnetization roasting-magnetic separation.
Here are some main processing technical methods of iron ore.
Magnetic separation is using a magnetic field to separate materials with different magnetic intensity. Magnetic separation is the most popular method used to beneficiate black metal ore. There are two kinds of magnetic separation, normal and high density. Normal magnetic separation is adopted to separate magnetite. High-density magnetic separation is used to separate hematite and other ore which is weakly magnetic.
The flotation is also commonly seen in nowadays iron ore beneficiation. It has become a very important way to recover weak magnetic ore. It is also used to treat iron ore fine to reduce the content of silica and impurities.
Flotation beneficiation separate ore at three physical statuses: gas-liquid-solid. The ore slurry enters the mixing bucket first. After the slurry is mixed thoroughly with chemicals, it is sent into the flotation machine. With water and gas fed into the flotation machine, along with the slurry, there will be bubbles generated. The bubbles take the parts which are valuable to us out of the slurry. And the rest is tailing.
The gravity separation separates ore parts with different density. Gravity separation is also one of the most popular ore beneficiation methods. It is widely used in weight metal ore beneficiation, especially weak magnetic iron ore.
Hematite, limonite, siderite and iron pyrites are very weakly magnetic. We cannot use normal magnetic separation to beneficiate. We have to magnetize them first. And then, we can use normal magnetic separation.
Magnetization roasting is a chemical reaction used in hematite beneficiation. It transforms Fe2O3 (weakly magnetic) into Fe3O4 (strongly magnetic). After magnetization, we can use magnetic separation.
It is a rather complicated process. There are many factors that can affect the effectiveness of the reaction. Actually, calculations can either reduce the iron ore or oxidize the iron ore.
Teresa Zheng
Mining& mineral processing | Gold CIL/CIP