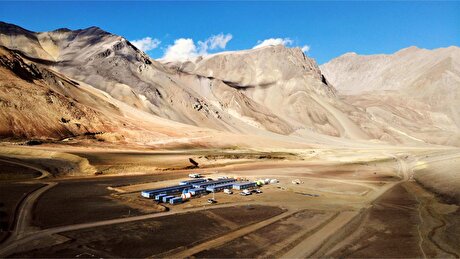
According to me-metals, Reza Khadem Kimiaei, explaining the performance and importance of implementing this project, said: The bucket boom reclaimer machine was designed using the world's most up-to-date technology and was manufactured at Azar Teyf Sepahan Company with an approach of maximum use of domestic manufacturing capacity, spending 50,000 man-hours. It was successfully installed, tested, and commissioned at Mobarakeh Steel without the presence of a foreign supervisor and with the help of domestic experts, spending more than 25,000 man-hours.
He emphasized: This machine, with a nominal capacity of 2,500 tons per hour, is capable of homogeneously and continuously harvesting more than 600,000 tons of pellets from accumulation parks 1 and 2, and provides the quantitative and qualitative sustainable harvesting and shipping of pellets required by direct recovery units 1 and 2.
The iron and steel development manager of Mobarakeh Steel listed the most important features of the machine as follows: concentrate and pellet extraction with a nominal capacity of 2,500 tons per hour; bench and chevron extraction capabilities; complete coverage of the material depot (47 meters wide and 12.5 meters high); ability to adjust the movement and material extraction capacity using speed control systems; anti-collision system to prevent collision with the material depot and adjacent machinery; use of a hydraulic brake system between the rail and bogie to stabilize the machine in emergencies; being equipped with a dry fog system to prevent dust dispersion; improved machine safety due to the use of two hydraulic jacks to change the boom angle; improved bucket wheel safety by installing a protective support; ability to adjust the operator's cabin according to the boom angle; maximum use of domestic manufacturing capacity (manufacturing more than 400 tons of metal skeleton).
In this context, some iron and steel development experts said the following:
Mohammad Hassani, Head of Ironmaking Line Development: The new boom reclaimer machine weighs over 550 tons and has a boom length of 48 meters. It is equipped with a drum-type cable collection system, two balancing jacks, and has an automatic central lubrication system.
Among the notable points in the design of this machine is the design of the rotating chute to allow simultaneous charging of both 02C05 and 02C05A tapes. Also, environmental compatibility and the installation of a dry fog sprinkler system are among the positive points of implementing this project, which will have a significant impact on dust control.
More than 400 tons of metal skeletons have been manufactured to build this machine, and the main material used to make these parts is S355J2N. The material cutting of these parts has been done using laser and plasma cutting, which has achieved high precision in fit-up and assembly and improved welding quality. Also, due to the sensitivity of the machine and the need to observe geometric tolerances and adaptations, maximum precision has been taken into account in the machining of the equipment by using modern methods such as Laser Tracking.
Seyyed Mohammad Habibi, Ironmaking Development Expert: Considering the movement of existing stacking and harvesting machines (stackers and reclaimers on site) as well as the presence of numerous conveyor belts in the vicinity of the boom reclaimer machine, numerous protective and safety devices have been considered, including 6 anti-collision system sensors in the boom and bucket sections with the ability to detect the approach of any equipment or material pile surface within five meters, a maximum boom torque sensor, a sensor to control the maximum force applied to the machine bridge, and bridge angle encoders, etc.
Another key safety feature of this machine is the wind speed sensor, which activates the locking system of the bogies to the rails when the wind speed exceeds the permissible limit, and at the same time, the wheels are locked and any movement of the machine is prevented, preventing possible damage and danger. The bucket holding system is also designed in such a way that in the event of any possible event that leads to the bucket being separated from the shaft and sleeve, the machine is not subjected to shock due to imbalance. Also, the installation of a four-load cell weighing device on the machine conveyor belt will provide the operator and the unit's production system with accurate information to control the amount of materials sent.
Seyed Saeed Mohtashamkhah, Assistant Expert for Ironmaking Development: Among the important activities of the project was the installation of the main boom of this machine weighing 100 tons. For this work, first two stands were placed at a height of 10 meters in line with the center of the machine perpendicular to the axis of the rails at a distance of 30 meters from each other, and then using two 360-ton cranes, while observing all safety and technical principles, the main boom was installed in its position on the stands in a short time. Then the jacks and the mast were installed, and after that the tension plates were connected to both the boom and mast structures. In the next stage, the jacks were electrified and the balance boom and the relevant tension plates were installed, and by placing concrete weights and reaching the required forces in the hydraulic jacks, balance was established and the stands were removed from under the boom. Next, mechanical installation and equipment, routing and cabling operations were carried out, and after the check signal, cold start-up and then hot start-up operations were carried out.
Hamid Bezaz, Head of Raw Materials Unit: Due to the decommissioning of the existing boom reclaimer, the accumulation and harvesting unit needed a new boom reclaimer machine to meet the needs of direct recovery units 1 and 2 during the pelletizing unit shutdown. This machine is a single-bucket harvester that is maneuverable and capable of sending materials from any point in the two parks 1 and 2 of the accumulation and harvesting unit and can send pellets and concentrate to the pelletizing and direct recovery units 1 and 2.
Other advantages of the new boom reclaimer include the improvement of the machine's safety and protection systems and the ability to adjust the operator's cabin according to the boom angle. It is worth noting that the implementation of this project improved production quality parameters, increased equipment availability, and reduced movement of mechanisms in the aforementioned parks in order to improve the unit's safety.
Reza Khadem Kimiaei, Ironworks Development Manager, concluded by thanking and appreciating the efforts of the staff of the Development and Management Unit and the Ironworks Area Operation Staff, the Supervisory Department, the Purchase Contracts, Development Planning and Support, Transportation, Azartif Sepahan Company, and all colleagues who participated in the planning, implementation, and commissioning of this project.