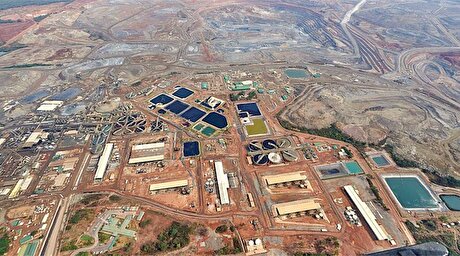
He added, “In this wastewater treatment unit, the wastewater undergoes garbage-removal, degreasing, aeration, chemical purification through hydrated lime [also known as slaked lime], ferric chloride [or Iron (III) chloride] and polyelectrolyte as well as the coagulation and flocculation processes before it is sent to clarifiers. Then it is used in the green space of the company after going through the carbon sequestration process and PH adjustment with sulfuric acid.”
He went on to say that particles in the wastewater, which are now in the form of sludge, are pumped into sludge collecting lagoons. After getting dry, they are sent on board trucks to a waste depot due to having a low percentage of iron (about 15 percent). “During the treatment process of industrial wastewater accumulated in the production lines of the Steelmaking Plant, the huge volume of waste and the low purity of iron, for which sedimentation of iron minerals and hydrated lime are to blame, can leave a destructive impact on the environment. It can also have a direct effect on rising transport costs, consumption of chemicals, and loading and unloading time in the lagoons dedicated to the removal of sludge.”
Navaei said the industrial and chemical wastewater treatment unit has put on its agenda efforts to recycle the wastewater and remove the existing problems, adding to reach that target, the unit studied proposed plans. Implementation of each plan brought its problems to light. Finally, a proposal was put forward on cutting the consumption of chemicals (hydrated lime) which would lead to improvement of environmental conditions and an increase in the purity level of iron in the waste output and its subsequent recycling.
He said the plan saw the wastewater produced in Mobarakeh Steel Company analyzed separately through the jar test [which is intended to simulate the coagulation/flocculation process in a water treatment plant] for about one year.
The findings of the yearlong lab-based research were presented in an article which was submitted in a national conference on clean water and was confirmed at the Energy Ministry’s Power and Water University of Technology, he said, adding it was later implemented on a pilot basis at the company’s galvanized refinery in coordination with the environment unit, the Iron-making Plant and the central laboratory for one year.
He described the implementation of the plan and its results as satisfactory and said that it was registered as a special project at Mobarakeh Steel Company, adding the implementation of the project did not come at a huge cost for the company. “Studies show that mixing part of the alkaline wastewater with industrial wastewater before it undergoes neutralizing and chemical processes will lower costs as far as transportation and repairs are concerned and will scale down the required workforce. It will also decrease the amount of hydrated lime used in the coagulation and flocculation processes, and will lower the consumption of lime, sulfuric acid, ferric chloride and polyelectrolyte.
“Finally, it will decrease the inconsistency apparent in the sulfate ion, and above all, it leaves no industrial waste at the treatment facility in the end,” he said.
The removal of lime, sulfuric acid and ferric chloride in the alkaline waste treatment system of the galvanized refinery can instead result in the use of the wastewater in the treatment facility of Unit 21, he said, adding, “Thanks to a decline in the consumption of chemicals in the industrial wastewater treatment facility, the outgoing waste is recyclable and can be used as raw material in the Iron-Making Plant.”
In conclusion, he thanked the management of the energy and fluid, environment and iron-making units as well as MSC’s central laboratory for their contribution to the project.