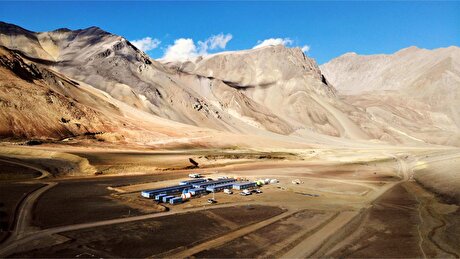
The Production Coordination System is responsible for making planning, setting timetables, making coordination between various production units of the Steelmaking and Continuous Casting Plants, as well as collecting production data and sending it to the executive information system (EIS).
In light of the fact that MSC had plans to raise its production of steel slabs to 7.2 million tons and add new units such as Casting Machine No. 5, Ladle Furnaces No. 7 and 8, and the Desulfurization Unit to the existing units, he said, the company needed to upgrade the Production Coordination System so that it can be applied to different functions such as planning and setting timetables for the melting in the plant, running labs, organizing the coordination procedures of ladles, controlling the ability of arc furnaces, running quality control of slabs, and calculating the melting temperature for the new units.
He said since PSC is a coordinator of level 2 electric arc furnaces (EAF), ladle furnaces, secondary metallurgy systems and continuous casting machines on the one hand, and is in connection with EIS system and automated systems of fluid energy processing unit on the other, its malfunctioning would bring production in the Steelmaking Plant to a halt. “That’s why implementation of this project and the operations to replace the old system with the new one was highly sensitive. Thanks to contribution of everyone involved in the project, close surveillance by experts at the plant’s automation system and successful implementation by the International Systems Engineering and Automation Company (IRISA), the project was properly carried out without interrupting the operations of the production lines.”
To undertake this project, the hardware architecture and operating system were fully inspected, he said, adding, “Then the operating system, databases, and applied programs were upgraded, the new production units were added to the system’s user pages and calculation algorithms, and the problems that existed in some of the previous calculation algorithms were corrected.”
Nasr characterized the indigenization of the system and its domestic implementation as an upside of the project and said, “The previous versions of the system in question had been implemented at MSC in cooperation with German and Italian companies. The current project was implemented by IRISA, as part of the company’s engineering projects, in cooperation with the Steelmaking Plant’s industrial automation team which also took care of the project’s technical and workshop-related supervision.
He appreciated the tireless efforts and cooperation of all those who contributed to the development and optimization of the Production Coordination System in Steelmaking and Continuous Casting Plants, among them: the management at the steelmaking, steel slab production, steel production units and technical production group, as well as those who were involved in launching the system, especially experts of level 2 automation at the Steelmaking and Continuous Casting Plants, management and experts of IRISA, staff of the technical production group, members of the company’s engineering group, technical services, production coordination, ladle furnace service, secondary metallurgy, arc furnaces, continuous casting, material handling, steelmaking lab, production control and planning, and quality control units.