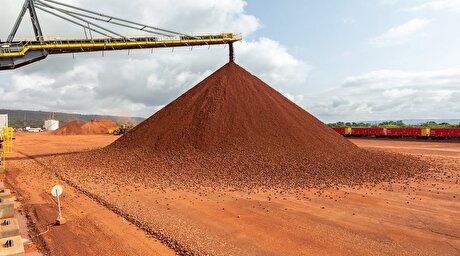
Currently, casting foundries mainly employ the polyurethane cold-box process to manufacture cores while inorganic core-making processes are gaining popularity. During the cold-box process, the reaction and the accelerated curing of the core are set off through the addition of a catalyst mixed with a carrier medium.
In inorganic core-making, however, this curing process is replaced by heating and purging with hot air, which causes water to evaporate and moisture to escape from the core box. It is a more complex and time-consuming process that is related to sand casting and curing, and is therefore subject to certain restrictions. This means that there are limitations on void spaces and geometry during inorganic core-making processes.
Nevertheless, a compromise can be found between core filling and core curing. Depending on the core geometry, an analysis can also show that the K+G core drying technology produces significant cycle time improvements in the cold box process. The patented Core-Drying Technology is integrated into the core box and can be fitted in new or existing moulding tools.