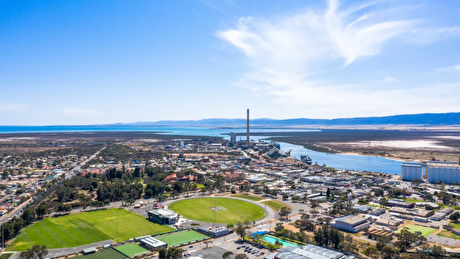
The Fill Future Zone was the hot spot for innovation at the world´s leading trade fair for metalworking, EMO, in Hannover from 16 to 21 September. The Austrian machine engineering experts presented end-to-end digitalization in metalworking in the sense of Industry 4.0. Intelligent simulation models (digital twin) create new opportunities in component development and production planning. Fill´s latest development, the syncromill u, as well as further developments of the syncromill c and syncromill h dual-spindle machining centers, were there to be seen, live on the Fill exhibition stand. During the course of EMO, Fill was presented with the 2019 Siemens ”Bring ideas to life” award.
“The symbiosis of virtual and real processes opens up completely new perspectives in production planning, material utilization, productivity, reliability, and system intelligence. The entire production process is elevated to a higher level,” explains Friedrich Dallinger, Head of the Metal Machining Technology Competence Center at Fill, on the sidelines of the trade fair.
The Upper Austrian machine engineering company managed to present a whole range of innovations at once in Hannover.
Intelligent technologies create an advantage
The Fill syncromill u21-63 machining center is particularly suitable for machining large-volume battery casings and framework components from profiles or castings. The intelligent machine concept allows component and customer requirements of new vehicle concepts to be ideally implemented. In conjunction with innovative clamping concepts, workpieces are machined extremely economically and efficiently. The many visitors on Fill´s exhibition stand were able to see this live for themselves.
syncromill c22-63/600
Dynamics, process reliability, and efficiency are the most important success criteria for the syncromill c22-63/600 machining center. Apart from one of the world´s shortest tool chip-to-chip times of 1.8 seconds, the syncromill c22-63/600 also sets new standards with a pallet change chip-to-chip time of less than eight seconds. The flexible machining concept enables extremely efficient, space-saving, and economical production of complex workpieces. Fill´s syncromill c22-63/600 was the machining center with the quickest tool and pallet change in this machine size at EMO 2019.
syncromill h21-63/500 with Sinumerik One
The Fill syncromill h21-63/500 machining center has been developed specifically for machining structural framework components (e.g. side members, cross-members, and crossbeams) from profiles or castings. This machine is equipped with the pioneering Sinumerik One controller and was presented to the public for the first time at EMO 2019. Siemens Sinumerik One is a particular highlight in the world of control technology. Thanks to its digital twin, Sinumerik One is the key element in the digital transformation and helps simulate and test work processes completely virtually. In this project, Fill is one of only a few machine builders worldwide to be involved as a development partner in Europe’s largest initiative in the field of big data. The syncromill h21-63/500 machining center is a key component of the project. In appreciation for the good collaboration, Fill was presented with the 2019 Siemens ”Bring ideas to life” award at an event during the course of EMO 2019.
Fill Future Zone
In an environment where rapid response to the market and high quality standards are decisive, the Fill Cybernetics smart factory solution provides the key competitive advantage. Fill Cybernetics connects to all the machines in a factory and enhances them with intelligent algorithms. This dramatically increases the profitability and quality of the entire production process. In parallel, production and process data is collected and recorded. This guarantees seamless component traceability. Platform-independent dashboards designed to meet customer requirements ensure an optimum overview and enable detailed analysis of products and machines. Availability is guaranteed and productivity increased.