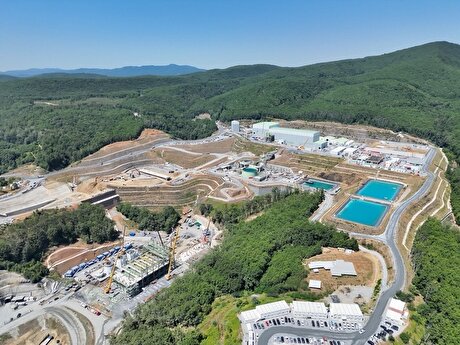
Aluminum melting and casting furnace (70 tons) at AMAG, Ranshofen
The aluminum industry assumes that worldwide consumption of rolled aluminum products will grow by 70 percent over the next ten years. With this dynamic growth in demand, AMAG started an ambitious enlargement program in 2012 with an initial volume of 220 million euros. In 2016, the company is additionally starting a new rolling plant project (strategy project "AMAG 2020"), with which the capacity should be boosted to more than 300,000 tons per year by 2017. The furnace ordered is part of this enlargement program. With the increase of rolling production, the quantity of production scrap also rises, which needs to be remelted. The furnace is designed for this task.
The tiltable melting and casting furnace is a joint development by AMAG and Hertwich. The first unit of this type has been taken into operation by AMAG in 2013. With a holding capacity of 70 tons this furnace was already of impressive size. The current furnace unit now ordered, with a liquid metal volume of 110+ tons, once again greatly exceeds the size of the existing unit.
The single-chamber furnace used for melting is able to also take over the function of a casting furnace, if necessary. For heating, two pairs of regenerative burners are installed above the melting bath level. With a specific maximum gas consumption of 500 kWh for each ton of aluminum the plant satisfies the strictest requirements, both in economic terms and also in terms of environmental impact. To ensure clean combustion an oxygen regulation system and separate regulating systems for natural gas and combustion air are provided. An electromagnetic pump ensures thorough metal circulation, constantly high melting performance and homogeneous temperature distribution in the furnace.
The scope of supply also includes a rail-guided, pusher-type charging machine (capacity: 25 tons), with which the furnace can be charged efficiently in only a few charging cycles.