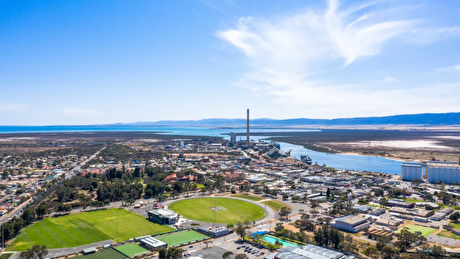
The JSPL Plate/Steckel plant in Raigarh after Danieli upgrading
Raigarh, January 12th, 2016 the JSPL newly furnished mill produced the first hot rolled coil.
With the target to overcome some quality limitations of the plant, to increase the productivity up to 1,2 Mtpy, to extend the product mix and to solve some maintenance issues of the mechanical equipment, in July 2013 JSPL awarded Danieli the contract for a major revamping project.
The revamping strategy was to renew the whole mill by installing new motors, stands, downcoilers, etc., whilst minimizing the shutdown times (please see details below).
The modernization was performed during two shutdown in July 2014 and December 2015.
During the first shutdown the machining of the 4-Hi Mill Stand was executed on site and adapting plates “liners” were applied to the existing equipment and piping to allow the mill to continue operating until the next scheduled major shutdown.
In December all the new mechanical and L1+L2 automation equipment were installed.
Accurate planning with off-line job execution and Danieli-JPSL team work have been the key of the success.
JSPL revamping data-x-items :