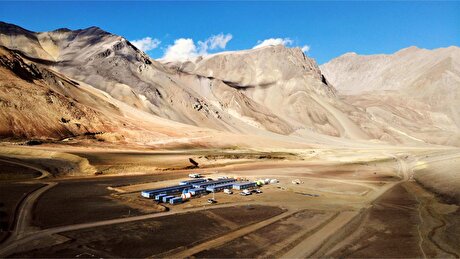
Among some of the giant experimental strides that the global iron and steel industry has taken in recent times to reduce carbon emissions, ensure energy efficiency and achieve flexibility in raw materials selection, the HIsarna process of iron making would certainly qualify as one. The DRI process of hot metal production combines the Cyclone Converter Furnace (CCF) for ore melting and pre-reduction and a Smelting Reduction Vessel (SRV) where the final reduction to liquid iron takes place.
According to Tata Steel, the technology removes numerous energy-intensive steps – including having to pre-process the ore and coal in separate coke, sinter or pellet factories. Test campaigns were conducted using steel scrap and biomass and created carbon reductions of more than 50%.
Tata Steel's chief executive of European operations, Hans Fischer, said: “HIsarna's results show we can make a significant contribution to improving the sustainability of steel production with this Tata Steel technology”.
“The development of this technology forges our ambition to become a steel company which is sustainable in all respects.”
The HIsarna process was developed in stages by Dutch steel giant Koninklijke Hoogovens and Tata Steel's IJmuiden works in The Netherlands. In 2004, the European Union brought pressure to bear on the steel industry to reduce its carbon footprint and, as a result, the Ultra-Low Carbon Dioxide Steelmaking (ULCOS) consortium was founded. Its purpose was to identify technologies that might help reduce carbon emissions of steelmaking by 50% per tonne by 2050. HIsarna is one of those technologies, which shows great promise and is the most advanced of the ULCOS technologies. Anglo-Australian metal and mining behemoth Rio Tinto had industrial-scale experience of the SRV process, called HIsmelt. An agreement resulted in Rio Tinto adding the HIsmelt technology to the cyclone furnace. The result was the HIsarna process.
In 2017, Tata Steel obtained the IP rights from Rio Tinto, now fully owning all HIsarna IP. Rio Tinto contributed its HIsmelt technology to the final design of the installation at IJmuiden, prompting the name HIsarna (‘HI' from HIsmelt and ‘sarna' from ‘Isarna', a Celtic word for iron).
The European steel industry has made significant progress in reducing carbon emissions. Currently Tata Steel emits 1.7 tonnes of carbon dioxide per tonne of steel produced at IJmuiden. Although it is still possible to find ways of further reducing energy use and carbon emissions, European steelmakers are slowly but surely reaching the limits of current technology. Achieving further reductions is only possible through development of breakthrough technologies. As one of the most advanced of ULCOS technologies, HIsarna undoubtedly is loaded with a lot of promise.
HIsarna's most important environmental benefits are the reduction of energy use and carbon dioxide emissions by at least 20%. Since the HIsarna installation produces almost 100% pure carbon dioxide, the gas is ideally suited for immediate capture and storage, without the need for a costly refining process. If governments choose to opt for this strategy, capturing and storing carbon dioxide could lead to an 80% reduction of carbon dioxide from the steel production process. HIsarna also allows for a wider range of steel production by-products to be reused, which will further close the loop of the steel manufacturing process. An additional advantage of HIsarna is the reduction of the emission of fine particles, sulphur dioxide and nitrogen oxide.
The HIsarna production process is more efficient than the BF route, as there is no need to pre-process ores and metallurgical coal. A complete production stage can be phased out: coking plants, sinter plants and pellet plants. This will also save a lot of energy, which is good for the environment and will lower manufacturing costs. HIsarna also enables the use of a wider range of ore and coal qualities, which will allow steel companies to produce the same high quality steels using cheaper and more widely available raw materials.
Meanwhile, the design of a HIsarna industrial plant has started. The industrial size plant will be two to three times the size of the current facility, capable of making up to 10 times more liquid iron. Experiments conducted with steel scrap and biomass at the pilot plant have revealed that it is possible to achieve emissions reduction of more than 50%. Identifying the ideal raw material mix, investigating options for recycling steel slag, investigating the possibility of recovering zinc and, most importantly, exploring options for capturing and storing carbon dioxide are the next big challenges.
Listen to this Technology at SteelVia- The Global Steel Innovations Forum
With sustainable steel production emerging as the one most crucial objective that can never be lost sight of, the game-changing HIsarna technology promises to offer solutions to many perennial problems dogging the industry. If you are keen to keep abreast of the unraveling of the revolutionary potential of this path-breaking technology, book your berth at SteelVia where Johan van Boggelen, Technology Manager, Research and Development, Tata Steel, Netherlands, will deliver an incisive and comprehensive presentation on the future potential of this disruptive technology.