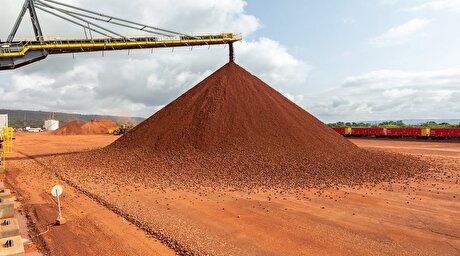
At just three days from hot startup the mill already demonstrated its full potential by rolling at 70% of its maximum capacity (including four strands slitting process) which will lead to a very fast rump-up learning curve
The rolling mill is designed to produce rebars from #3 to #16, smooth (rounds and squares from 1/2” to 2”, and merchant bars, including angles, channels, flats from 1” to 3”, and T-profiles.
The 20-pass mill is fed with 160- and 180-mm square billets in cold charge and hot charge mode with direct transfer from the conticaster.
The rolling mill is mainly comprised of H, V and H/V convertible cartridge-type stands, with quick stand change system for the intermediate and finishing mills, followed by a QTR-Quenching and Tempering line for rebars.
A 100-m-long cooling bed with layer forming system completes the hot processing line.
The cold finishing area includes an in-line straightening and cold shearing system.
Rebars finishing is performed with three automatic counting and bundling stations, with 11 tying machines for sub-bundles, six tying machines for master bundles, and two tying machines for bent bundles.
Merchant bars and sections are processed in 24-m automatic stacking station with six strapping machines.
The process technology provides for up to 5-strand split rolling of rebars.
Danieli Automation provided fully integrated Lev1 and Lev2 automation and process control systems, and a Hi-Profile for in-line hot measurements of bars size tolerances.
This is the fourth complete Danieli minimill installed at Deacero, for a total eight rolling mills for bars, wire rod and merchant bars.
Another important step in the 50-year successful relationship between two teams with a win-win attitude.