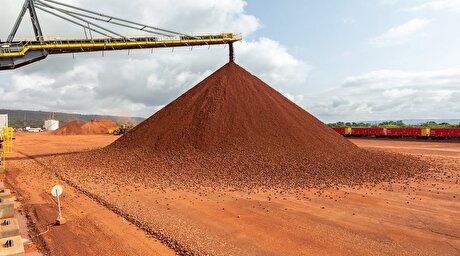
This is true for rolling of flat and long products, as well as for the automation and process controls applied to optimize production. Guests attending the Aluminum and Non-ferrous session at the Fourth Danieli Innovaction Meeting learned of the market forces involved in these sectors, as well as various successful applications. These included:
“Nonferrous metals market outlook, 2017-2022,”” a presentation by Mr. Julian Kettle of Wood Mackenzie, a global leader in commercial intelligence for the energy, metal and mining industries, provided an overview of present trends impacting the nonferrous metals markets, and an outlook on expected demand / price evolution, specifically for aluminum markets through 2019/20.
“Aluminium vs. Steel in Automobiles,” surveyed the influence of stricter emission standards in the emergence of new or improved production technologies, and how this has resulted in increased usage of aluminum in cars. Mr. Goran Djukanovic, a renowned analyst and industry consultant, provided an insight to the latest developments and trends in automobile lightweighting.
“Trends in aerospace,” a presentation by Mr. Stefan Raufeisen, Program Manager for New Aircraft Generation of Airbus Research & Technology, provided an insight to the developments in the aerospace sector and highlights for future metallic airframes, with a special focus on expectations for material suppliers, and overall supply chain outlook.
“A global approach for solving rolling process challenges,” reviewed the challenge facing rolling mill operators to make products that simultaneously meet the requirements for sustainability, product quality and low production cost. Innoval Tegnology, the technological process experts of the Danieli Group, is developing new technologies to enable better use of recycled aluminium, without loss of quality. Physics-based models of many aspects of the rolling process have been developed and provide lower energy costs - but with no loss of quality, and other models have led to both a reduction in environmental impact and higher product quality.
“K-Maps: knowledge management with added value,” described the importance of managing a company’s knowledge resources and making these available to employees who need it is a key aspect of operating a successful fabrication plant. But, where shall you start?
Innoval has developed a robust and repeatable approach that is based around an easy-to-use visual format that provides a secure system for managing and delivering your know-how.
We also can supplement your in-house expertise with Innoval’s own knowledge, as a way to shorten qualification times for new products, such as automotive sheet.
“AMAG and KUMZ: the two most modern aluminum flat product plants” presented reviews of the technological features developed for two projects recently executed by Danieli. Following the needs of AMAG and KUMZ, Danieli engineered, manufactured and successfully commissioned two hot rolling mills, one cold mill, and a stretcher. The close relationship of the teams made it possible to address the market requirements of both customers and to increase the technological know-how of Danieli.
“The benchmark cutting and slitting technology over the last 70 years,” summarized the progress in tailor-made solutions that led to modern slitting applications, new product characteristics and the high-performance lines. Danieli Fröhling’s know-how and capability to customize line concepts and designs are important to fulfill individual product mixes and the material flow requirements of producers. The dedicated approach takes into consideration market requirements and end-user’s experiences when developing new concepts in line design, and this helps to ensure best-in-class performances in terms of quality and productivity.
“Digital Twin: from kinematic simulators to cyber physical systems” considered simulation and virtualization as very effective and low-cost technologies for testing and training in operational situations, particularly in the industrial environment. Over recent years Danieli Automation has continuously developed a portfolio to satisfy the requirements for safer, more efficient and easier operations. Two products stand out: the iStand, an advanced kinematic simulator; and QLive. Each one represents a new generation of virtual reality and high-fidelity modelling, and both give the possibility to estimate in advance and in detail the technical impact for CapEx and OpEx optimization.
“Sural, Quebec: the most competitive endless rod mill for the widest range of aluminum series,” profiled this Danieli line now in full operation, reflecting the most flexible, advanced and efficient technology available now for producing a broad range of aluminum alloy rods, both for mechanical and electrical applications. The design was conceived to explore the production of new alloys rod not yet on the market. The entire process is managed by an intelligent control system that supervises the production schedule, plan set up and quality control for a flexible and repetitive process. The package of technical solutions and control adopted permits OEE in the range of 90%.
“Advanced heating and control systems for aerospace products” studied how aluminium offers one of the best displays of quality standards plus lightweight characteristics for the aerospace industry. To reach all the necessary requirements in compliance with the most restrictive aerospace standards (e.g., AMS-2750E, RPS-953, Nadcap, etc.), different technological processes must be applied. Danieli Olivotto Ferré has a complete furnace portfolio to support all the heating and heat-treating phases, starting from melting/holding to homogenizing, annealing and ageing. Also, the furnaces achieve a fully automated process, with superior control system accuracy for the highest process reliability and repeatability.
The ESED 4.0 CHP-Compact Hydraulic Package system is an evolution of the ESED-Energy Saving Electrical Drive (launched in 2012) that makes it possible to reach the same performances in terms of extrusion speed with a lower number of pumps. The extruders of aluminum alloys, who have endured the difficulties of construction and building industry, have been compelled to re-adapt their company strategies, and face the change as an opportunity for growth, instead of an inauspicious event.
Energy saving is an important factor when choosing an extrusion plant, being one of the parameters leading to the OpEx reduction, which depends as well from running cost due to normal wearing and relevant maintenance downtime.