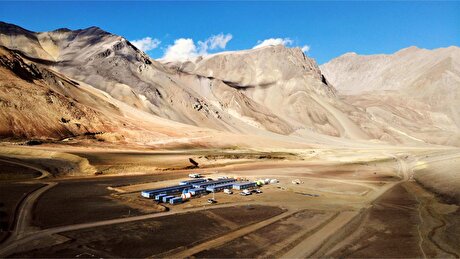
The success comes as the volume of water used in Ukraine's Arcelor stands at 8.5 cubic meters per ton; as for Germany's steelmakers, it is 8.3 cubic meters; and in hot rolling plants and companies that produce flat steel products in the world, it is 8 cubic meters, the MSC chief said, adding MSC uses 7.73 kg of refractories for every ton of molten steel it produces, whereas the global average is 25 kg.
Recalling the role of productivity in raising the status of organizations, he said productivity might be defined differently by different institutions; what all definitions have in common is minimization or prevention of waste which decreases the proportion of output to input. In today's competitive world, the productivity-related issues can either help promote the status of organizations or seal their fate.
Dr. Sobhani said organizations which boast agile human resources and are capable of protecting themselves against external factors such as an increase in the cost price of their products, an increase in the prices of energy forms and market slump can be hailed as enjoying productivity. In the absence of high productivity and proper strategy, organizations become loss-making as it has been the case over the past two years.
He said over the years, especially the past two years which were very tough years for the steel industry around the world, MSC has suffered no losses. On the contrary, inauguration of expansion projects has resulted in reasonable profits for the company.
The MSC managing director went on to say that in his company productivity, cooperation, organizational cohesion and order have become intrinsic parts of a culture, adding all members of staff do contribute to higher productivity, as a result, MSC shines like a star in the sky of the country's steel industry and has made a name for itself on the world stage.
He further stated that when a company is said to enjoy 90 percent productivity, there is as much as 10 percent waste in that company, so the management and staff members should join hands to work out plans to push down waste levels.
The MSC chief described the inauguration of Sangan Pelletizing Plant in the east which produces 5 million tons of pellets on a yearly basis, the success Hormozgan Steel Company has pulled off and completion of an expansion project at Saba Steel Complex as achievements of his company in recent months and said such achievements are a source of pride for the entire industry and the Iranian nation.
He further said low production capacity, which pushes down productivity, is a major problem Iran's steel industry is faced with, adding we need to keep in mind that at low capacity, companies cannot be economical because infrastructure and human resources are as costly in a small production unit as they are in high-capacity plants. In big organizations, though, high productivity pushes down the cost price to a large extent.
One way for steelmakers to overcome challenges and become productive is to make sure their capacity and production scales are economically-driven, Dr. Sobhani further said, adding that economic-centeredness should be credited for the edge MSC holds over other steelmakers.
He went on to say that MSC alone accounts for half of all steel produced in the country, while 10 other companies produce the remaining 50percent. High overhead costs and low capacity tamp down their profit margins and sometimes put them in trouble.
The MSC managing director described shortage of graphite electrodes as one of the biggest problems steelmakers around the world are faced with and said the fact that graphite electrodes are in short supply constitutes a major problem, the resolution of which requires steelmaking staff to make more optimal use of such electrodes.
Recalling the good track record of his company in cutting energy consumption, he said MSC is in a better position than its global rivals when it comes to consumables such as water and refractories. However, that does not mean we should not make more efforts and develop more plans for a better future.
He said controlled procurement and management of stored spare parts help prevent capital from sitting idle in storage facilities, adding such measures are instrumental in cost management and productivity improvement.
Dr. Sobhani said production of data-x-items for which demand is low, a production decline as far as weight is concerned and an increase in the volume of data-x-items which directly find their way into storage facilities do play a role in pushing down corporate productivity.
When we aim to produce 7 million tons of steel products on an annual basis, we need to keep in mind that any single percentage of production which is not in line with our stated goals finds its way into storage facilities and will eventually have to be sold at a price lower than the price those who place an order for a certain product are ready to pay. Such a practice will not only reduce the company's profits, but will result in a decline in its production quality level. At the same time attention should be paid to production quantity.
As far as productivity in production of pellets, direct reduction, casting and hot rolling is concerned, MSC is very close to its rivals, he said, adding in recent years MSC has made progress on all fronts, especially products which are warehoused. But there is still more room for progress and efficiency levels can further improve.
As for MSC productivity when it comes to human resources, the MSC chief said in recent years his company has managed to maintain its human resources and thus raise productivity. Creation of new capacity in our expansion projects has helped us narrow the gap with rivals.
In conclusion, the MSC chief thanked the personnel of the steel giant for their tireless efforts in the past to achieve the company's stated objectives and said he hopes the same endeavors help MSC achieve its goals in the current year.
According to the correspondent of the Steel Newsletter, the MSC deputy director for technology presented a detailed report on the performance of different units in the same ceremony and said in the 12 months to March 20, 2017 MSC's per capita proposals registered an increase over the year before. During the same period transformation committees approved of more proposals, the number of projects increased, contribution of the personnel to the transformation projects got a boost, so did the quality control system and the number of knowledge-related registrations.
Manuchehr Nikfar further said the under-roof project of Saba Steel Complex is 95 percent complete. Calcined lime furnaces of Hoz-e Mahi Mine are 98 percent complete, while Sangan's iron concentrate project and the small-scale power plant of Saba Steel Complex are 50 and 49.7 percent complete, respectively.
He further said the wastewater treatment network of Mobarakeh and Lenjan is 81 percent complete. Besides, expansion deals on the hot rolling projects of Shahid Kharrazi facility and Hormozgan Steel Complex are on the verge of being signed.
In conclusion, he said the level of personnel satisfaction with the conditions of the company has been on the rise over the years. He also touched on the criteria taken into account in naming productive employees and wished all staff members health and success.