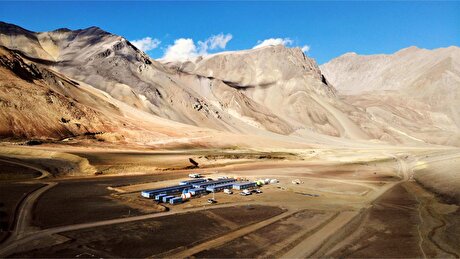
According to Me-Metals, Mohammad Ali Rahimi said in this regard: Thanks to the grace of God, the support of the organization's managers, the good cooperation of the colleagues located in the production units, repairs, technical office, workshop, technical safety, management and repairs of cranes, the company's support units and contractors, the stoppages caused The energy limitations turned into an opportunity to rebuild the equipment, and the long-term planned maintenance operation of machine number 1 was implemented within 20 days.
He said: complete mapping and alignment of lines with a laser tracker and replacement of rollers, modification of columns supporting rollers, replacement of soft water cooling system piping, replacement of pushers and line repellers, modification and replacement of grease and hydraulic pipes, upgrading of precision instrument sensors in hydraulic pump stations. And the servicing of all electrical equipment was one of the important activities that was carried out safely by the hardworking central and local maintenance contractors of Lom and the contractors based in the district.
According to Rahimi, the last old cutting machine of the casting machines, which had not yet had the opportunity to be replaced, was replaced in this shootdown with a new cutting machine with a unique design, which is the result of continuous optimization by the capable experts of mechanics, electricity and automation of this unit and a masterpiece in the machine industry. The cross-section of Takthal was in the country and the region and added another golden leaf to the Diwan of honors of Mobarakeh steel.
The head of continuous casting repair of module B further explained the unique features of this machine in the new design: the new cutting machine is equipped with a movement system to control the position of the torch and machine servo drive, which replaces transverse jaw clamps with a sliding vertical clamp with PreClamp capability to increase accuracy. Longitudinal table (combination of Germany's Framag design and China's Xian design) and being equipped with a motor separating clutch for smooth machine movement can improve the quality of cut surfaces while increasing the longitudinal accuracy of the table.
Dost Mohammadi, mechanics technician of foundry repairs: thanks to Altaf Elahi and the efforts of colleagues in continuous foundry repairs and the approach of foundry management in improving the quality of production plates, in several phases, the repair of one shot down machine was carried out in 20 days:The first phase, carrying out the health activity of the equipment, oscillator, set of segments, stretching and straightening rollers; The second phase, carrying out the mapping activity of the casting line; The third phase, carrying out the activity of replacing defective water pipes; The fourth phase of checking the hydraulic circuit and fixing defects; The fifth phase, carrying out chatting and line element activities.
In the shadow of the aforementioned activities, the installation of a new cutting machine as well as the optimization of the equipment, including the shifting table, pusher and disappearing rolls, were successfully completed.
We thank the participation and cooperation of the technical office, the central repair shop and the repair team of PM and Aroco and the production team and the cranes unit.