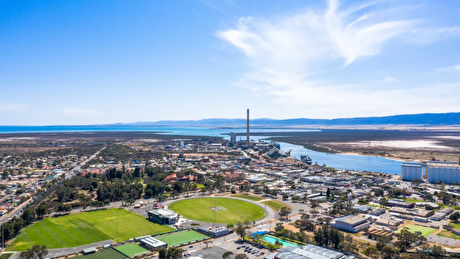
The project team of SSAB and SMS group with Heikki Nisula, General Manager Maintenance and Investments at SSAB Europe, Hämeenlinna, Finland (4th from left).
SSAB has awarded SMS group an order covering the modernization of a continuous pickling line entry section in its Hämeenlinna plant. This modernization will significantly increase the line’s availability and its output as well as the degree of automation and safety. Especially with the installation of an X-Pro® laser welder with fiber laser and of a high-performance tension leveler it will be possible to produce modern, high-strength steel grades with high alloy contents. The conversion, including modification of the complete electrical and automation equipment, to be accomplished in two phases is scheduled to be completed by the end of 2018.
“Together with SMS group we will make the line fit for the future and upcoming challenges,” says Heikki Nisula, General Manager Maintenance and Investments at SSAB Europe, Hämeenlinna, Finland. “The new equipment will make sure we can process materials with yield points of up to 900 megapascals. Higher capacity at lower operating costs will be a further benefit.”
An essential element of the modernization is the X-Pro® laser welder with solid-state laser. Contrary to a conventional carbon dioxide laser, the laser beam here is generated in a resonator by means of a laser-active fiber. Thanks to its high efficiency and good controllability, operating costs will decrease by up to 90 percent. A crucial feature of the new system is its simple, modular and nearly maintenance-free design. Additional major advantages of the X-Pro® laser welder are its patented inductive pre- and post-treatment of the weld, automatic adaptation of the welding parameters on the basis of a material melt analysis and an integrated automatic weld seam monitoring system. The machine also impresses with its short cycle time of less than 60 seconds.
“Already in 2015, at the Laser Strip Welding Symposium, SSAB had had difficult-to-weld, high-alloy plates from its own production welded by a machine with fiber laser. The result was very good,” says Heikki Nisula.
The modernization will take place in two phases. In the first phase, the new entry section will be installed on part of the present coil storage area while pickling line production will be going on. The entry section will comprise two payoff reels, the X-Pro® laser welder and a horizontal six-fold looper. In the course of a one-week downtime, the new equipment will be connected to the pickling line by means of a bypass running across the existing entry section.
In the second phase, also during ongoing production, the existing entry section will be removed and replaced by a new scale breaker and a recuperator tank. The scale breaker will be specially designed to process high-strength strips. If so required, the maximum strip tension can be raised to up to 900 kilonewtons. The recuperator tank will serve to pre-heat and pre-clean the strip with spent acid from the pickling process before the strip enters the actual pickling line. This will increase the capacity of the existing turbulence pickling section. Integration of the new plant components is scheduled to take place during a two-week downtime at the end of 2018.
All new equipment will be supplied by SMS group including the electrical and automation systems. Additionally, the level-2 automation system for the complete pickling line will be modernized. Prior to commissioning, the automation system will undergo a Plug & Work integration test in Germany to simplify commissioning and ensure safe and fast plant ramp-up after the downtime. The efficiency of the pickling line will be further increased by installing the SMS eco-production turbulence pickling model.
The line is designed for strips with thicknesses between 1.5 and 6.5 millimeters and widths from 650 to 1,650 millimeters. In the processing section, the strips will be pickled in the turbulence pickling tanks at a speed of up to 180 meters per minute, whereas the maximum strip speed attainable in the entry section will be 400 meters per minute.
The X-Pro® laser welder with fiber laser to be integrated into SSAB‘s new entry section will provide high efficiency and availability, and a safe, fast and fully automated process even for difficult-to-weld materials.