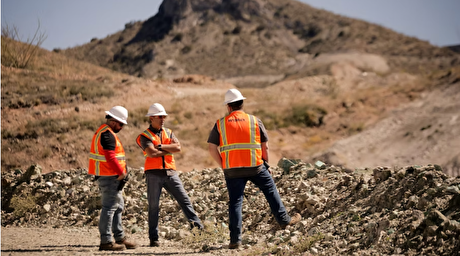
Photo of a comparable CONTIROD® line.
RYKER BASE PRIVATE LIMITED, a joint venture of Polycab Wires and Cables and Trafigura, India, has placed an order with SMS group for the supply of a CONTIROD® CR-3500 line.
The line for the casting and rolling of wire rod in a single process will have a production capacity of 35 tons of cast and rolled copper wire rod per hour. Commissioning of the CONTIROD® line at the JV’s new plant in the Indian state of Gujarat is scheduled for the first quarter of 2018.
On the CONTIROD® CR-3500, RYKER will produce predominantly ETP copper wire rod (Electrolytic Tough Pitch) as starting material for its own cable production.
The in-house production of eight millimeters drawing stock on the new CONTIROD® line from SMS group will enable RYKER to supply a consistently high product quality for the existing ultra-modern wire drawing plant. RYKER will thus be able to achieve a high product quality over the whole process chain.
Thanks to the use of modern, energy-efficient installations (such as lambda control on the shaft furnace, AC motors, deoxidization and cooling section with separate media circuits) and high performance, the new CONTIROD®CR-3500 from SMS group will establish the preconditions for achieving the aspired goals.
The scope of supply includes a shaft melting furnace, a twin-belt caster, a 12-stand rolling mill with separate individual drives, a deoxidization and cooling section, a wire coiling station, a strapping unit and a film packing station.
The shaft melting furnace employs the SMS group’s proven lambda control system in combination with the further developed charging and distribution system for cathodes and recycled scrap. This technology minimizes natural gas consumption and increases product quality.
The twin-belt caster produces a rectangular cast ingot with 6,300 mm² cross-sectional area in a practically horizontal casting process. This is an important precondition for a high and consistent quality of the finished products, in particular with the demanded large dimensions.
The homogeneous cast ingot is formed into the required wire rod dimensions in the twelve individually driven stands of the rolling mill.
The casting and rolling technology employed establishes the very good preconditions required for the downline drawing process – particularly for the production of enameled wire and multi-fine wire in an environment with constantly growing demands on drawing speed and technological properties.
In the cooling section, the oxide layer on the surface of the wire is first reduced by a chemical reaction with a water/alcohol solution before it is cooled to the desired target temperature in a second step using water without the addition of alcohol. The separation of the two process steps allows for a significant reduction in alcohol consumption.
CONTIROD® is a registered trademark of Aurubis Belgium.