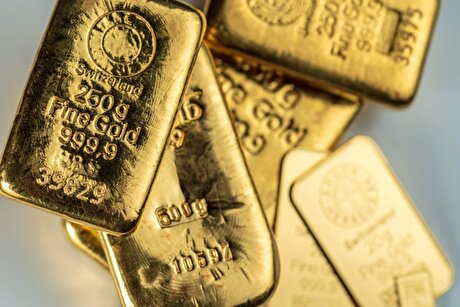
Counter to that, scrap intensive secondary castings usage will fall as the shift to full battery electric vehicles occurs. In the coming years, EVs will support primary aluminium demand and impose a limit on scrap demand.
40 million EVs by 2030 and 10 million tonnes of aluminium demand
CRU forecasts global battery electric (BEV), plug-in hybrid electric (PHEV) and hybrid electric (HEV) sales to increase to 42 million vehicles by 2030. From a share of 4% in 2017, we expect electric vehicles to account for approximately 30% of the global vehicle fleet by 2030.
A “greening” of global power and now, increasingly, transport markets has begun: sales of New Energy Vehicles (NEVs), for example, grew by more than 40% year on year globally in 2016. These global trends will have potentially decisive impacts on aluminium markets.
CRU has developed a comprehensive forecasting and scenario evaluation tool with which to understand these impacts and the policy, technological, macroeconomic and societal factors which shape them. This model incorporates a consistent macroeconomic framework, and considers developments in technology and power markets.
In this piece, we provide a summary of the key findings for aluminium demand from EVs. We estimated aluminium intensity through discussions with car makers, tier 1 and tier 2 automotive suppliers and information from automotive fairs. We complimented this research with desk based research of investor material and conference presentation from key industry players.
Plug-in hybrid and full battery electric vehicles use 25-27% more aluminium than the typical internal combustion engine car today. This assumes 160kg of aluminium per vehicle as a base line for aluminium content in internal combustion engines.
Increases in aluminium usage in Internal Combustion Engine (ICE) cars is in great part because of the light weighting benefits of aluminium. This was clearly the driver for Ford’s F-150 switch to aluminium and underlies much of the move from steel to aluminium bodied cars.
However, for EVs the increase in aluminium usage has as much to do with new applications, as increased adoption of aluminium body sheet.
CRU has developed a EV aluminium intensity model broken down into four categories:
E-drive: encompassing housing for e-motors, DC-AC inverters, DC-DC converters, chargers, heat-pumps and reduction drives.
Batteries and battery housing: covering battery casing for prismatic batteries, battery foil and battery housing. Battery housing is the biggest volume element of this market. Car makers are yet to decide the standard for battery housing, and we incorporate a combination of predominantly steel housing (Mitsubishi Outlander PHEV and Nissan Leaf BEV), cast aluminium battery housing (Audi PHEVs) and a combination of extrusions and rolled products (Tesla Model S).
We have two additional categories which exist in internal combustion engine vehicles:
BIW and closures: We split this category, which covers aluminium automotive body sheet. Current EV models are more aluminium intensive than current ICE. However, two developments are threatening aluminium body sheet uptake from EVs. Firstly, improved battery technology reduces the need to light weight. Secondly car makers are now designing EVs from scratch, rather than converting ICE models, which increases the driving range. Cars such as the Nissan Leaf and Tesla Model 3 are less aluminium intensive than previous models. Nonetheless an undershoot in battery advances, will be a boon to aluminium sheet to light weight and extend range.
Common with ICE: CRU estimates there is just over 60kg kerb weight from ICEs which will be present in all EVs, which is brakes, steering, heat exchangers and wheels. In addition, plug-in and hybrid electric vehicles retain the engine supporting secondary castings demand.
Aluminium extruders are hoping for their F-150 moment, which propelled aluminium body sheet into the mainstream. EVs, and particularly battery housing gives the largest potential upside to aluminium extrusions usage in EVs. More modest gains for extrusions will come in existing applications, such as trim and crash management systems.
However, companies such as Magna and Nemak are hoping to dominate battery housing with cast aluminium solutions. These companies are key aluminium engine part suppliers today and need to adapt to the shifting automotive landscape.
Castings Armageddon looks some way off – a universal shift to battery electric vehicles and for engines to disappear. Plug-in and hybrid vehicles will retain the engine and support secondary aluminium castings demand. Importantly, excluding used beverage cans, car engines are the main market for end of life aluminium scrap. We examine the knock-on impact to scrap markets in full in our Aluminium Long Term Market Outlook.
Rollers should be betting against great leaps in battery technology and extended driving range. For the previously mentioned castings and extrusions applications aluminium is the most suitable material. For rolled products, it is mostly the light weight benefit.
Primary aluminium producers and indeed the LME price have great potential upside from EVs. No primary producers today are exposed to the secondary castings market. A wholesale shift to battery electric vehicles will boost primary aluminium demand at the expense of aluminium scrap.
In addition to our long term demand outlook to 2040, the CRU Aluminium Long Term Market Outlook presents production and capacity data by smelter and a primary aluminium market balance by region. For further information on CRU Aluminium Long Term Market Outlook which was released in late December 2017, as well as other products from CRU which focus on the aluminium market contact us via the button below.