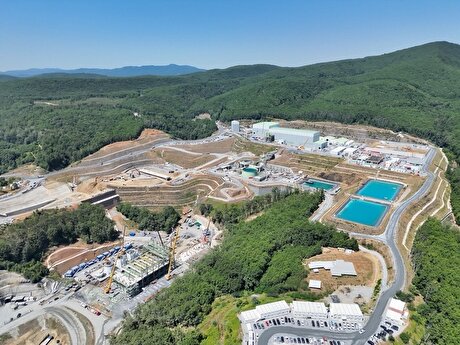
In January 2018, one of the two lines in 1+1+3 configuration, i.e. two reversing roughing stands and a three-stand finishing mill, received a further finishing stand. SMS group completed the line expansion to 1+1+4 configuration during a shutdown period of only 23 days. The first coil was successfully rolled on January 26, 2018, one day ahead of schedule.
Installation of the new mill stand in position F1 of the finishing train.
Being in position one of the finishing train, the new, high-performance stand accomplishes the major part of the forming work. The new stand F1 is of 4-high design, like the three existing stands. It features latest actuation and control systems, such as CVC®plus (Continuously Variable Crown) roll shifting technology, a rolling technology package specifically designed for aluminum hot rolling and X-Pact® electrical and automation systems. The technology package includes a wide range of technological features such as hydraulic actuation systems and cooling, lubrication, measuring and cleaning systems designed to achieve the required mechanical properties and an excellent strip surface quality.
Along with the installation of the additional finishing stand, SMS group modified related plant equipment to make it suitable for the new and higher product quality requirements and for the increased line capacity. Especially for low-temperature rolling, a newly developed blow-off and suction system has been installed in the exit section of the finishing mill. The newly added finishing stand provides the line the high flexibility needed to roll the complete range of aluminum hot strip grades in widths up to 2,900 millimeters and thicknesses between 2.2 and 12 millimeters.
Tianjing Zhongwang Aluminium was very happy about the fact that the high-capacity hot rolling line could resume regular three-shift production only three days after commissioning.
The first aluminum hot coil rolled in the expanded finishing mill.