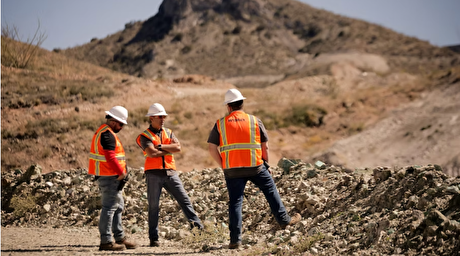
With this upgrade Impol Group Slovenia has invested in the future viability of the cold rolling mill and has brought about significant improvements. The range of coil dimensions has been extended, including larger coil diameters and increased width, with maximum coil mass doubled. Higher strip tensions now allow thicker strip to be rolled. What’s more, the strip quality conditions, particularly the thickness and flatness results, have been improved. Last but not least, strip drying has been optimized resulting in an enhanced strip surface quality.
To achieve these improvements, SMS group has modified the foundations and replaced the complete entry and exit equipment. The new pay-off and tension reels are fitted with mandrels with outboard bearing supports to ensure safe handling of the larger and heavier coils. Thanks to the new change-speed gear units at the drives in the entry and exit sections and at the main drive, thicker-gage material can now be rolled with higher torques. Also new strip threading equipment has been installed.
On November 25, 2018, the first aluminium coil was successfully produced on the cold rolling mill revamped by SMS group.
The pay-off reel features a strip centering system from EMG Automation GmbH, a company of SMS group. This allows the rolling process to be optimally controlled. The aluminium strip can be guided through the rolling mill perfectly centered, a key requirement for a stable and precisely wound coil.
Along with the rearrangement of the tension reel on the exit side, a belt wrapper was integrated. The design of the belt wrapper allows strip coiling with the strip being fed from above or below. While improving coiling of the rolled strip, this design also provides higher flexibility in the production of treadplate.
Integrating thickness gages at the entry and exit side of the mill has improved the quality of strip gage control. New spray headers for work roll cooling and a new flatness measuring roll provide enhanced flatness and quality control. A DS system (Dry Strip system) arranged in the exit section of the four-high mill stand reliably removes any residual oil from the strip surface. This ensures that the strip surface is of a very good quality, a key requirement for successful downstream processing of the aluminium strips.
The revamp also included the installation of new ancillary coil handling equipment and utility systems. This involved the integration of new coil cars, a pallet conveyor system for coils complete with a strapping station, and media supply systems for the hydraulic and pneumatic equipment.
In this revamping project, the main challenge for SMS group was to design the new components and plant units in such a way that they would fit into the existing configuration, while ensuring that the revamped equipment would comply with the latest European machinery safety standards. Last but not least, the good cooperation between all involved was key to the success of the project. The aluminium cold rolling mill of Impol Group Slovenia is now fit for the challenges of the future and certainly stands comparison with the performance of a brand new plant.
The project team is glad about the successful revamp of the aluminium cold rolling mill, which is all set for more challenging rolling tasks.