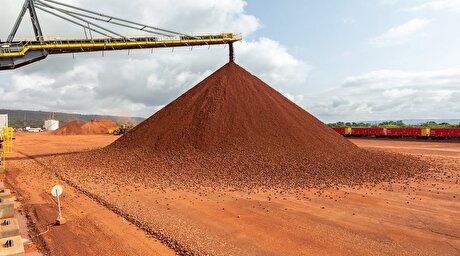
For the converter shop, SMS group will supply two 350-ton BOF converters, two 350-ton ladle furnaces and one 350-ton RH TOP vacuum recirculation degassing facility (Ruhrstahl Heraeus). The environmental engineering will include two primary waste gas cleaning systems with a dry dust collection system and a secondary waste gas cleaning system for the converters, ladle furnaces and the RH facility. The secondary gas cleaning plant with bag filter is designed for a capacity rating of more than 3,400,000 Nm³ per hour.
In order to increase energy efficiency, the converter shop is equipped with two heat recovery systems for generating steam from the waste heat of the converter primary gas. The produced steam is fed into the works pipeline network. Furthermore, thanks to the installed gas extraction technology, a volume of more than 400 million Nm³ converter waste gas per year can be used to replace other fossil fuels for energy generation. Not only the energy costs but also the output of CO2 can thus be reduced considerably. Here, use is made of the tried and tested SMS group adjustable skirt for the recovery of the energy-containing CO gas. The X-Pact® electrical and automation systems for the complete converter shop ensure efficient production and a high quality of the steel produced.
India’s largest BOF converters of their kind are equipped with the maintenance-free lamella suspension developed by SMS group, with bottom-stirring systems for combined blowing and with tilt drive systems manufactured in the SMS group’s own workshop.
The single RH-TOP vacuum plant from SMS Mevac is provided with a modern ladle lifting system (RH-RockerType®), which hydraulically – and supported by a counterweight – lifts the ladle towards the vacuum vessel. The RH facility is equipped with a multifunctional TOP lance which can be used as an oxygen blowing lance under vacuum for steel treatment and as an atmospheric oxygen burner lance for heating up and holding the temperature of the RH vessel. Two ladle transfer cars ensure short cycle times. The RH facility will be equipped with an extensive alloy addition system.
The SMS group scope of supply and services will include engineering, manufacturing and delivery of the mechatronic equipment, the X-Pact® electrical and automation systems and the supervision of erection/installation and commissioning.
Commissioning of the converter shop is scheduled for 2019. In the future, more than five million tons of steel per year shall be produced by the new plant.
At the JSW Dolvi works near Mumbai, SMS group has already erected an integrated steel plant with steelmaking facilities and a CSP® plant for JSW.
JSW is one of India's leading steel Producers.