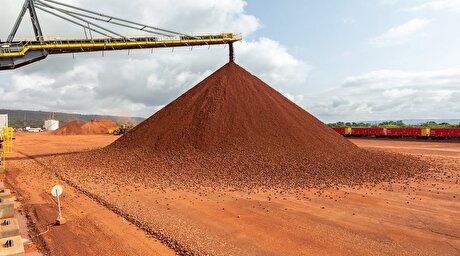
Iran’s largest scrap car recycling plant was inaugurated in Zanjan Province last week.
Inaugurated by deputy minister of industries, mining and trade, Mansour Moazzemi, the Fuka San’at plant was established with an investment of $6.51 million and an annual production capacity of 180,000 tons of scrap iron.
The German Scholz Holding GmbH holds an 80% stake in the plant and the rest has been financed by an Iranian partner.
Founded in 1872 and based in Essigen, Germany, Scholz Holding collects, sorts, processes, sells and recovers steel scrap and nonferrous metal. The company produces and supplies aluminum and high-grade steel, according to information by S&P Global Market Intelligence, a division of S&P Global.
“Three local steel companies have already signed deals with Fuka San’at to pre-purchase the produced scrap,” Nasser Faghfouri, the head of Zanjan Province’s Industries, Mining and Trade Organization, was quoted as saying by ISNA.
For years, Iran’s steel industry has struggled with a shortage of scrap iron.
According to experts, Iranian steel mills’ annual demand for the raw material stands at about 3 million tons, while local scrap producers can only supply half this figure. The country’s ports also lack the infrastructure to import large volumes of scrap iron.
Experts argue that higher scrap iron consumption can help boost the steel industry’s competitive edge by enhancing efficiency. However, Iran’s unbridled direct-reduced iron production and the material’s high availability discourage producers from increasing scrap usage.
According to Seyyed Taqi Mortazavian, an industry expert, Iranian steel mills use two types of foundry melting furnaces, namely induction and electric arc furnaces. The two types have different energy consumption rates based on the feedstock used in them.
Arc furnaces differ from induction furnaces in that the charge material is directly exposed to an electric arc, and the current in a furnace terminal passes through the charged material. About 70-75% of Iranian steel are made using EAF.
Induction furnaces, on the other hand, are ideal for melting and alloying a wide variety of metals with minimum melt losses. Since no arc or combustion is used, the material is heated to a temperature no higher than what is required to melt it. This can prevent the loss of valuable alloying elements.
The use of EAFs allows steel to be made from a 100% scrap metal feedstock, which greatly reduces the energy required to make steel when compared with primary steelmaking from ores.
Induction furnaces are also highly efficient in scrap melting. No harmful pollutants are emitted during the melting process and induction heating spreads throughout the furnace efficiently, which speeds up the operation.
“In both furnaces, the melting operation will use less energy, if scrap is used instead of DRI. This would consequently reduce operational costs,” SMT daily quoted Mortazavian as saying.
The expert noted that EAFs use 400-435 kWh with scrap iron as feedstock. This figure jumps to 600-635 kWh when DRI is injected. The same scenario is true for induction furnaces, in which the use of full DRI feedstock needs 1,100 kWh while scrap usage requires less than half that energy.
Iranian steel mills’ annual demand for the raw material stands at about 3 million tons, while local scrap producers can only supply half this figure.
In Iran, cheap energy and abundance of iron ore are the main causes of steelmakers shying away from scrap usage,” he said.
“This is while most Iranian iron ore is made up of low-grade hematite deposits, the use of which entails a costly beneficiation process. The less pure the mined ore, the higher the volume and more energy is required to turn it to steel.”
Mortazavian pointed to the example of Turkey, a regional steelmaking rival.
“Turkey has considerably higher energy prices compared to Iran but the neighboring country is a net importer and producer of scrap iron. Even though it predominantly uses EAFs, it still has a lower finished price than Iranian mills,” he said.
According to Mohammad Holakouee, managing director of Tuka Trading Company, scrap metal currently makes up less than 15% of Iranian mills’ annual feedstock.
His company is a supplier of raw materials for the industry and works with heavyweights such as Mobarakeh Steel Company.
“Using scrap iron is definitely more efficient, but the market supply is low in the face of rising demand and the government has not taken any measures to address this issue,” he said.
“Boosting scrap supply, through other than government patronage, requires a lively construction sector, which is currently deep in recession,” he said.
There is also the issue of quality for the available scrap there. According to Shahram Saber-Tehrani, the head of Khorasan Steel Complex’s Research Department, scrap metal collection and sorting are usually handled manually in unlicensed scrap yards across Iran.
Utilizing this outdated method keeps the country’s scrap metal supply below the required industrial level.
Furthermore, recyclers forgo the crucial process of separating clean from dirty scraps. Hence, steelmakers are compelled to feed their mills with low-quality, environmentally unfriendly scraps while struggling with an unbalanced supply and demand chain in the process.
This is while, according to Holakouee, Iranian industries, especially the auto sector, have high scrap metal production capacity which, if harnessed while complying with global industrial standards, can enhance the steel industry’s output by cutting production costs and increasing product quality.
“Currently more than 4 million write-off cars in Iran, with 350,000-400,000 more being added annually, in addition to 30,000 trucks, buses, minibuses and tractors, need to be scrapped,” he said.
“Cars alone can potentially provide the industry with about 10 million tons of scrap metal.”