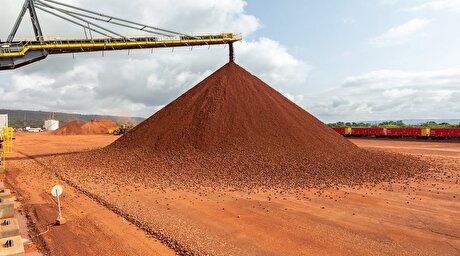
How was this made possible?
After customer solicitations related to the development of an appropriate technology to help them to better apply the ISO 8501 – 1, Winoa took on the challenge to find the appropriate technical solution to fit with the customers’ requests, considering that all of the working specifications of their daily manufacturing processes are driven by very strict ISO regulations.
After investigating the market, patenting the usage of analytical colorimetry for cleanliness level evaluation of the blasted parts, developing prototypes to be used by key industrial users and obtaining their agreement, Winoa submitted a report to ISO committee for approval. The pillars of the report were the working principle of the analytical colorimetry, the instruments specifications, a documented example about how it can be used in the analytical colorimetry as a support tool in the assessment of the cleanliness of the steel substrates at the end of the blasting process. This stage was fulfilled with the support of the company's Technical Test Center located in France. Another key element was the study cases representative for several industrial applications that may be concerned by the assessment of cleanliness level of the blasted parts.
• The steel pipes manufacturing for oil and gas industry, where the cleanliness level is one the required parameters to be validated after the blasting process, before to step to the next stage of process and namely the epoxy coating application.
• The cast iron automotive part for cast iron foundry, to control the quality of the desanding operations.
• The trailers manufacturing, to control the cleanliness level of the blasted parts prior to galvanization.
• The freights wagons, to control the cleanliness level of the blasted parts prior to coating applications
• The cold drawn bar producers, to check the optimization of their descaling operations.
Available for commercialization
For the moment, it’s promoted through Winoa's internal commercial networks. Please get in touch with Winoa's local commercial teams, or take up direct contact via the W Abrasives website: www.wabrasives.com
Stay tuned for upcoming Winoa developments! Soon, WA CLEAN technology will be functional via a smartphone with the possibility to generate instant quality follow-up reports of your blasting process, everywhere and at any time with the WA Clean 2.0 version.
WA CLEAN device already adopted by the end users
The WA CLEAN Technology is an electronic optical device using as working principle the analytical colorimetry to support the visual assessment of the surface preparation grades of uncoated steel substrates as defined in ISO 8501-1 or in SSPC – VIS 1.
This technology made the proofs in several industrial fields, and can be also used to reduce the extra blasting time, saving money and improving the quality level by fending off the eventual over-blasting phenomenon that may install and could affect other important surface preparation parameters to be achieved after the blasting process, such as the roughness level.
The WA CLEAN device has been developed in order to help the end users to better implement the ISO 8501-1 standard. To avoid any misinterpretation, the goal of the device is not to replace the ISO 8501-1, but to support the appropriate implementation of the latter one. The novelty and in the same time one of the main benefits provided by the WA CLEAN device is that from now on, the validations of the surface preparation grades via visual assessment by using the ISO 8501 – 1s reference photographs are reinforced by figures issued from measurements done with the WA CLEAN device on the initial visually qualified surface preparation grades. The usage of WA CLEAN device will allow to implement a quality follow-up on the blasting process in terms of cleanliness level of the blasted parts.