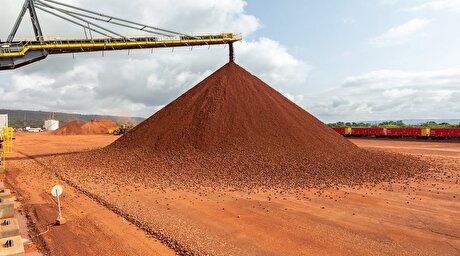
Glass production in Iran dates back to World War II when the first glass factory was built in Tehran, the Persian daily Forsat-e Emrooz reported.
“The need for glass is permanent. At present, nothing is holding us back from production. There is only a slight problem with data-x-items that remain unsold in warehouses,” says Mohammad Ali Qanbari, the head of Tehran’s Glass and Mirror Sellers Union.
Glass production is different from the rest of the industrial activities in that the machinery is turned off in other factories when there is no production, but the glass furnaces are always burning.
“In the 18 to 20 years, which is the lifespan of an industrial furnace, it is never turned off, because the melted material inside will become as hard as stone and the device cannot be used again. This is why glass production is a constant and ongoing activity, and sometimes the supply-demand balance is disturbed,” he says.
Iran’s glass industry is capable of meeting the domestic need and the country is 100% self-sufficient in this respect.
“Repairing and running the machinery is carried out by experts at home and there is no dependence on foreigners,” he said.
According to Qanbari, there are eight large-scale factories across the country using fully-mechanized machinery together with professional workforce.
They produce a total of 400,000 to 500,000 square meters of different kinds of glass, including bulletproof, double and multiple-glazed, security, curved, decorative and table top glass as well as mirrors. “Even though the process is automated, between 200 and 300 people work in each production unit.”
Forty percent of domestic production are exported to neighboring countries, Central Asia and even European countries such as Germany, Italy and England.
“Energy is expensive in Europe and wholesale production is not economically sound. Therefore, they ask for Iranian glass and glass products that are on par with international standards and enjoy high quality.”
Silica is the raw material used in the industry, which is found abundantly in the country.
According to Qanbari, the ongoing recession in the construction sector has negatively impacted many businesses, including the glass and mirror industry.
Masihollah Oveysi, an old hand in the business, says running a glass workshop is a very difficult and arduous profession and that the dangers involved, including those pertaining to the handling of glass products, make it unappealing to many; “so it is not a job for everyone”.
He is not satisfied with the market conditions and believes people no longer have that extra money to spend on decorative objects and their priority is with foodstuff and apparel.
“Our major problem is the recession in construction sector, which directly affects our job. The other problem is that architects and builders now go straight to UPVC window manufacturers to provide for their need and no longer come to glass workshops with orders. This has largely limited our work,” he said.
According to Oveysi, the minimum space needed to start a business is a 100-square-meter plot of land for the workshop, in addition to another smaller place dedicated to where the business owner deals with customers and accepts orders.
“Some of our colleges have now equipped their workshops with automatic cutting machines which, using computer software programs, carry out the tasks of measuring and cutting the pieces of glass without the slightest error.
As these cost more than one billion rials ($28,700 at market exchange rate), not everyone can afford them,” he concluded.