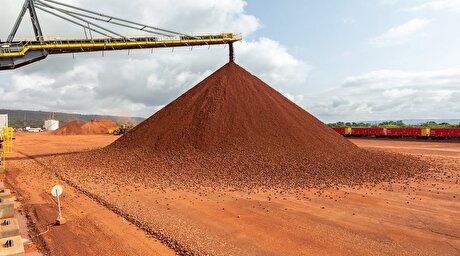
How easy it is to mine lithium (just add salt), just how much of it there is in Nevada (enough for 300 million EVs), how to be environmentally friendly (“put the chunk of dirt back where it was”) and, given these facts, why miners haven’t been trying harder.
Since lithium is “just like widely available”, according to Musk and Tesla’s scientists, they have eliminated other hard to come by metals like graphite (replace it with sand, obvs) and cobalt from batteries (at least in theory), Musk’s prime raw material worry is nickel.
Nickel and dimed
Ahead of Battery Day, in an investors conference call Musk had a big shout-out for all the nickel miners out there, wherever they may be in the world (hopefully near some nickel):
“Well, I’d just like to re-emphasise, any mining companies out there, please mine more nickel. Okay. Wherever you are in the world, please mine more nickel and don’t wait for nickel to go back to some long — some high point that you experienced some five years ago, whatever. Go for efficiency, obviously environmentally friendly nickel mining at high volume. Tesla will give you a giant contract for a long period of time, if you mine nickel efficiently and in an environmentally sensitive way. So hopefully this message goes out to all mining companies. Please get nickel.”
Nickel was languishing below $10,000 a tonne five years ago, not exactly an incentive price, but whatever. Mine efficiently and at high volume? We should give that a try, fellas! Then we can make up in volume what we lose on price.
At Battery Day Musk also ended the mining lesson with a plea for nickel. Perhaps the world’s miners did not get the previous shout out because this time Musk said he personally called all the CEOs of the biggest mining companies.
OR BUILD THE EQUIVALENT OF 23 MINES LIKE SUMITOMO’S AMBATOVY MINE IN MADAGASCAR – AT $8.5 BILLION A POP
Musk did at least end that auspicious day in the Tesla parking lot on a cautiously optimistic note: “It is very important. I think they are going to make more nickel.”
They better – a couple of days after the event Musk confirmed in a tweet that Tesla will reach production of 20 million vehicles per year before 2030.
MINING.COM used data from Adamas Intelligence, which tracks demand for EV batteries by chemistry, cell supplier and capacity in over 90 countries, to calculate the deployment of raw materials in Tesla cars on a sales weighted basis in 2020.
By extrapolating those numbers, the company’s use of raw materials, if it was producing 20 million cars a year instead of the 500,000 vehicles it made last year, was determined.
Tesla’s models use on average around 45 kilograms of nickel (NCA and NCM811). The numbers are based on the assumption that roughly 20% of Tesla newly sold cars would be equipped with LFP batteries through 2030.
And if, as expected, Tesla moves to NCMA chemistries in China, nickel use would go up slightly and cobalt would go down marginally.
When Tesla makes 20 million cars in a year it will need more than 30% of global mined nickel production in 2019 (2020 saw a 20%-plus reduction in output) for its batteries.
Put another way, Tesla will have to buy the entire output of the top 6 producers – Norilsk, Vale, Jinchuan, Sumitomo, Glencore, BHP, and then some.
Or build the equivalent of 23 mines like Sumitomo’s Ambatovy mine in Madagascar – at $8.5 billion a pop. Obviously, money is no object for Musk, but still.
Get it to nameplate capacity and you only have to build 12, but you’ll have to torture that orebody until it gives you straight mineralogy and ore grades so that you’re not constantly reconfiguring the plant. This is not just an Ambatovy problem – but a common feature of nickel mines, and no, that’s not why it’s called the devil’s copper.
But China’s nickel pig iron and stainless steel makers won’t give up that supply so easily.
And besides converting 0.9% nickel ore to battery grade material cheaply and efficiently at high volume may be beyond even the rocket scientists at Musk’s Space-X. (And if the cyberpunktruck makes up a big portion of the 20 million, Tesla is going to need lots of stainless steel too.)
That leaves Indonesia, where a number of high-pressure acid leaching (HPAL) projects using deep-sea tailings placement (DSTP) are in development. HPAL operations will likely become a significant source of new supply for the battery supply chain.
But HPAL and DSTP are not exactly the type of acronym you’d want the prospective TSLA buyer who’s in it for green credentials to learn if you want to get to 20 million. If you think artisanal mining in the Congo is a bad ESG look, you wouldn’t want images of the red shores of Basamuk Bay to enter the popular imagination.
Since Tesla is replacing graphite anodes with silicon, it’s not necessary to dwell on the fact that if this elusive scientific breakthrough is not commercialized at the speed of a Tesla in Ridiculous Mode, the carmaker would need 94% of the world’s natural graphite production by the time it hits 20 million cars a year.
At least you can make more graphite.
Likewise, with cobalt – the metal that dare not speak its name at Tesla – the requirement of more than half the globe’s production before 2030, is irrelevant (at least in theory).
Similarly, it’s not worth mentioning that global lithium production was only 77,000 tonnes last year, and Tesla needs 127,000 tonnes annually to make 20 million vehicles. Because, Nevada.
Apart from nickel, a potential headache for Tesla20m is rare earths, 90% of which come from China.
Some three-quarters of Tesla’s motors use permanent magnets and should the ratio stay the same the company will need nearly 40% of magnet rare earth mined output (MagREO – NdPr, Dy, Tb) according to Adamas, which also publishes a rare earth handbook and tracks the metals in EV motors.
But, as every popular science article ever written about rare earths says in the first paragraph, despite being called rare earths, they are not.
In fact, the 17 elements are more abundant in the earth’s crust than lithium.
I guess you could say rare earths are just like widely available.