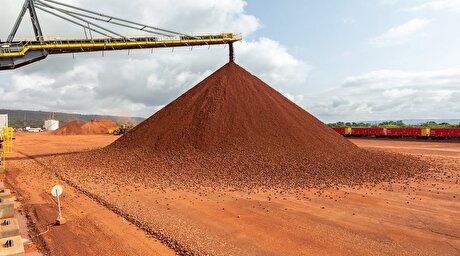
The modernization of the hot strip mill, established in the 1960s and supplied by a Soviet manufacturer, was scheduled to be implemented during several shutdown periods until mid-2020.
Within the modernization scope, SMS group equipped the finishing stands with new hydraulic adjustment systems and work roll bending systems. These powerful actuators enable MMK to produce strips within close geometrical tolerances. In addition, SMS group installed new equipment for changing work and backup rolls and a new high-pressure hydraulic system for the finishing stands. The modernization allows MMK to expand the portfolio of the plant, to improve product quality and reduce operating and maintenance costs. The rolling mill capacity will rise by 500,000 tons per year.
Also part of the large-scale project was a completely new X-Pact® automation system from SMS group, which was first installed in the SMS group test center for testing and pre-optimization under realistic conditions in line with the Plug & Work concept. The automation system includes basic automation elements and process models such as X-Pact® Pass Schedule Calculation for roughing and finishing stands, the Profile, Crown and Flatness Control X-Pact® PCFC, the X-Pact® Cooling Section Control model for strip cooling, a pacing system for the entire hot strip mill, the X-Pact® Vision operating and visualization system as well as a wide range of measuring equipment.
SMS group furthermore renewed the drive technology of the finishing mill and supplied six main drives including converters, two new spur gears and six mill pinion gear units as well as new drive spindles.
The revamp strategy provided for the modernization to be implemented during several shutdowns until mid-2020. Due to the present crises caused by the COVID-19 pandemic, great demands are made on all parties, not least the companies fighting to maintain the economic performance, and hence for a speedy return to normality.
MMK used the lower sales volume to be expected due to the crisis and decided, at the end of February 2020, to realize the great repair shutdown in its hot strip mill 2050 despite adverse circumstances and while respecting the health measures required by law.
Existing travel restrictions in Russia and the European Union presented additional obstacles. However, at the end of March, based on an almost 100-year-old trusting relationship, the CEOs of both Management Boards agreed per video conference to initiate allnecessary steps to procure, by means of special permit, visas for a group of selected experts and to grant them entry to the region by charter flight. The group was joined by a team from GE Power
Conversion, the supplier of the main drive converters and a long-term partner of SMS group, who provided maximum support in this situation.
In cooperation with customer MMK, additional options for remote support and augmented reality assistance were implemented. Thanks to the infrastructure established with the X-Pact® Service Portal, the customer could contact software experts and technologists at numerous SMS group locations for the solution of his problems.
Both, work performance and the smooth handling of the project have only been possible thanks to the trusting cooperation of all parties involved. So, SMS group would like to take the opportunity to express its sincere thanks here.