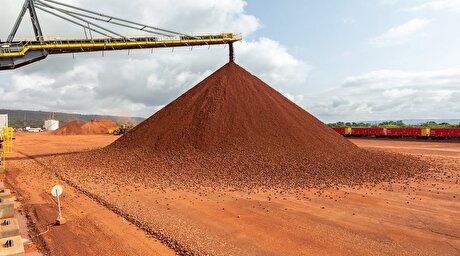
At the beginning of 2018, ZEISS acquired a majority share in BOSELLO HIGH TECHNOLOGY, the Italian specialist for industrial X-ray systems. ZEISS, thus, strengthened its competence and worldwide presence in 2D and 3D X-ray solutions. ZEISS VoluMax F1500 thunder is now the first jointly developed computer tomograph (CT) for automatic inspection in production and thereby combines the expertise of both companies: The sophisticated design of the system comes from Bosello, the advanced evaluation software from ZEISS.
Like all CTs in the ZEISS VoluMax family, the system is characterised by its robustness, which guarantees reliable quality assurance in production environments. In order to achieve the greatest possible efficiency in production, the compact CT can be flexibly integrated in the smallest space according to the individual requirements of the respective production line. The system is also - and this is unique on the market - equipped with an automatic conveyor loading system that feeds the parts directly through the CT. With only eight seconds per part for loading and unloading, downtimes are reduced to a minimum. The actual scan time could be down to 36 seconds, depending on the part.
A coherent package: hardware, software, service
Like all systems from ZEISS, ZEISS VoluMax F1500 thunder comes with software. This fits seamlessly into the entire production and quality assurance process. The ZEISS Automated Defect Detection (ZADD) evaluation software is particularly valuable for users. Not only does ZADD detect such defects as cavities, cracks or pores, it also classifies and locates them. However, the greatest advantage for the user lies in the evaluation of the defects: the software indicates whether a detected defect will cause problems during later production steps. This enables manufacturers to sort out defective parts reliably and precisely. If individual defects occur frequently, customers can also intervene in the production process earlier and avoid increased rejects.
Thanks to its robustness, ZEISS VoluMax F1500 thunder requires very little maintenance. If problems should arise, the simple configuration of the system allows users to correct minor errors themselves. If necessary, ZEISS service is also available worldwide - with technicians on site and all spare parts on stock. This means that production can be restarted quickly.
Foundries and manufacturers who want to sustainably increase their productivity and reduce costs receive optimum support with ZEISS VoluMax F1500 thunder.