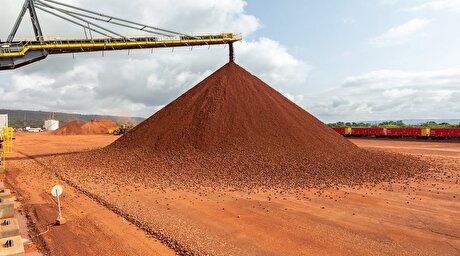
BY GERHARD KRAUSKOPF, BUCHEN / ODENWALD
In the foundry sector, molding sand is mainly processed in mixers with vertically mounted whirling mixing tools. This also applies to the Ludwig Frischhut foundry in Neumarkt-Sankt Veit, which has been part of the TALIS Group since 2010. Here, the mixing tool TuneMixx takes over the preparation and mixing process of the sand components. With the use of this system, not only was the mixer extremely quiet, a higher degree of preparation or energy savings was achieved, but also a significant increase in throughput.
The Frischhut foundry in Neumarkt-Sankt Veit processes its synthetic molding sand in an inclined intensive mixer. Extreme vibrations of the previously installed star swirler led to cracks on the mixer frame over a longer period of time. In order to get a grip on the vibrations caused by imbalance, the maintenance management has decided to use a market innovation, the TuneMixx mixing tool system from Krauskopf Maschinentechnik from Buchen (Fig. 1).
Frischhut manufactures molded parts made of spheroidal graphite and lamellar graphite, which are required for water and sewage supply. The castings are processed in our own facility in Pfarrkirchen and are coated with epoxy powder using the environmentally friendly fluidized bed or spray process. On behalf of the customer, cast parts are also machined, coated and checked up to 25 bar internal pressure using custom CNC machining centers. The cast parts are shaped on two molding lines: a line from Künkel-Wagner, Alfeld, with the molding box dimensions 620 x 520 x 200/220 mm and from Heinrich Wagner Sinto, Bad Laasphe, with the molding box dimensions 1250 x 900 x 400/400 mm, with a nominal sand requirement of 28.5 t / h.
By 2015, however, the sand preparation had provided just under 60% of the required amount of sand. The conversion from a conventional whirler to the patented TuneMixx system alone reduced the preparation times by almost 40% and consequently increased throughput in the same order of magnitude. From this point on, the molding plant could be supplied with sufficient molding sand. "An absolutely worthwhile investment that exceeded our expectations many times over," said the maintenance manager at the time, Alois Spiegl. The TuneMixx system was initially purchased in order to eliminate the vibrations on the mixer and the associated damage due to the precise concentricity. This requirement was met in every respect, of which the management took a look at the mixer platform.
Encouraged by the success in vibration elimination and an increase in throughput, the molding sand properties were examined in an independent test laboratory. The results revealed other positive aspects. With the TuneMixx system, it was possible to increase the degree of preparation to 100% and to reduce the sand agglomerates previously contained to almost "zero". The continuous improvement processes (KVP) usual for Frischhut in terms of energy saving even placed the mixer with the TuneMixx in second place after one year of operation, because the savings from the new mixing tool brought about a 45% reduction in electrical consumption compared to the one previously used conventional swirler. So far, the fact that all the wetted parts in contact with the product, such as mixing blades, floor tools, etc., can be exchanged or turned over in a matter of seconds due to a hydraulic clamping system installed in the TuneMixx system, has remained completely unmentioned (Fig. 2).
As a result, the foundry's production downtime was reduced from several hours to a few minutes. Krauskopf, originally started with the goal of carrying out maintenance work on a vertically operated mixing tool quickly and easily, can look back on more than 30 units after a successful market launch of the mixing tool TuneMixx, not only in foundry molding sand processing, but also in the refractory industry, in the glass sector, in the building materials sector, and in carbon industries or metallurgy. Another advantage is the variation and combination options in the design of the mixing blades. The profile, cross-section, length and wear material can be individually adapted to the mix, and tested flexibly with the quick-change system, since time-consuming and personnel-intensive revision downtimes are no longer necessary for a change (Fig. 3).
This is how Frischhut started to use the mixing blades made of chrome chilled cast iron. Initial results showed that wear is greatest in the lower area and higher-quality wear protection is definitely appropriate. From there, mixing blades with globular tungsten carbide armor were used, which have proven their worth in the cost-benefit calculation to this day. The axially symmetrical construction of the mixing blades also helps to save and conserve resources - they can be used on both sides and therefore twice. In addition to Frischhut, other companies have long since given way to influencing procedural parameters by processing with a TuneMixx as well as the "quick change system" hygiene factor. The mix quality, the throughput, and the reduction of the temperature input due to shorter mixing times are a very important reason for many plant operators to use the mixing tool. The mechanical engineering company Krauskopf Maschinentechnik GmbH & Co. KG, founded in 2013, develops, manufactures and sells mixing tool systems, spare and wear parts, as well as individual wear protection solutions for various mixer brands and industries at the Buchen im Odenwald location. Measurements, service and assembly work as well as procedural advice on site are also part of the company's tasks.