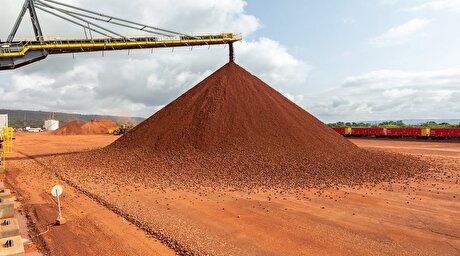
Gaining control over foundry processes, being able to ensure the final quality of the components by solving production problems in real time or developing lean and energetically efficient processes are the ideal goals of any foundryman. Also, to standardize knowledge about its own processes, usually dispersed among diverse figures and machinery, to keep it inside the organization is a very attractive aim for any foundry.
But some factors regarding HPDC processes, such as the limited amount of well-trained foundrymen, the harsh process conditions given inside the cavity (high pressure and speed, mold-melt reaction,…) as well as other conditions like the spraying make it difficult to capture and analyze process data for further exploitation.
In that scenario, the closest many aluminum foundries find themselves from jumping into 4.0 is limited to process control data facilitated by industrial equipment that, even though one could think that suppose a solid and robust starting point, is far from reality. It is common that equipment from diverse brands provide different kinds of data and ratios; this also happens among different generations of machinery from the same brand. In addition, it is usual that data cannot be extracted from the cell or that there is no way to accede to a historic data storage.
Then, as a starting point, the problem is not that the aluminum foundry has no data to begin with, it is even worse: aluminum foundries find themselves in front of incoherent and non-comparable data. Data that cannot be centralized and, of course, data that might not give relevant information about the aspects wanting to monitor and/or to improve. All these aspects are fundamental, not only to approach a 4.0 strategy, but also to analyze any production problem or process failure or incoherency.
Then, being able to obtain reliable, accurate and standardized process data seems to be a necessary starting point to develop a 4.0 HPDC strategy. But, where to begin?
As a technology center strongly linked to industrial companies, at IK4-AZTERLAN we have accompanied several HPDC foundries approach big challenges that were too overwhelming for them. A lack of method, no specific knowledge or not enough dedication-time are usually the biggest barriers. Among the 4.0 industry projects we have developed along with our customers we can find a wide variety of them, from data digitalization and traceability projects to the deploy of tailored mold by mold predictive control systems. To do so, our aluminum casting experts back on our artificial intelligence and ICT expert team, which is devoted to the efficiency of metallurgical processes.
Building a scalable 4.0 HPDC strategy
To map out a rational and scalable 4.0 strategy (this meaning that the budget to implement such is limited and results and ROI oriented), the aluminum foundry should, in first place, identify the critical process phases aiming to gain control over. The capacity to focus will help the foundry figure out which process data are relevant and, therefore, which ones need to be monitored and analyzed. That way, the foundry will be able to size the data capture project.
As a minimum, capturing the injection curve and some temperatures would be a basic starting point for any aluminum foundry, but the backbone to standardized comparable data history for a HPDC process relies on a specialized measuring system independent of brand or machine generation. Of course, foundryman’s knowledge about their own processes will be a necessary input to identify relevant parameters but relying on external expert support should not be disregarded.
Once target and dimension are defined, the data capture strategy will be approached. For this purpose, the foundry needs to identify which process data are reliably offered by production cells and which process steps will need of further data capture systems or sensors. Of course, a sensor implementation strategy must be thoughtfully designed since the sensor should be the closest to the relevant phenomena aiming to control, but simultaneously the service life of the element should be ensured. As noted before, data coming from different sources must be translated to a language of comparable and compatible variables.
For all those reasons, complementing this information by an external high-quality data collector that works with any machine family is highly recommended. To achieve that, trustworthy sensorics, such as those built by ELECTRONICS GmbH offer a wide range of data management opportunities.
Among the sensors that can be applied to the HPDC process there is a wide range of them, from basic sensors measuring parameters such as hydraulic pressure or plunger stroke, to some more advanced ones, that permit to go deeper into the process, like those oriented towards the capture of mold surface temperature, cavity internal temperature, cavity internal pressure, vacuum pressure, vacuum air flow, die release flow, cooling circuit temperatures and flows, etc. The information gathered from this sensor network can also help the foundry plan maintenance work or detect irregularities in mold closure or column effort, among others.
All the process data captured by the specialized sensor array will be centrally stored so a production data history can be checked and analyzed by foundrymen. Ideally, a real time performance information will be obtained so process deviations can be corrected with the help of an alarm system. On the one hand, a historic record will help HPDC process experts identify correlations between parameters producing both, positive and negative results, and detect optimum performance ranges. An easily accessible history should also address several main aspects of the process such as its stability and when a maintenance action should be performed. Real time information will permit to act over specific ongoing production problems detected.
With the help of industry 4.0 technology experts, this knowledge will later be translated into high added value tools like Predictive Control Models and Machine Learning systems driven by Artificial Intelligence built on advanced data architecture and algorithms.
Conclusion
Bonding HPDC expert knowledge and accurate process data management, regardless of the level of automatized output that the aluminum foundry aims at achieving, is a fundamental starting point to reach an efficient management and production. A robust 4.0 HPDC process can be no other but the reflection of a reliable data capture and analysis method, as well as a firm bet of the foundry to dominate its processes.
An independent advanced sensor system that will capture and centralize process information along the plant in a comparable language is a necessary starting point to settle a stable basis to approach an industry 4.0 transformation project and will help the foundry learn about its own processes.