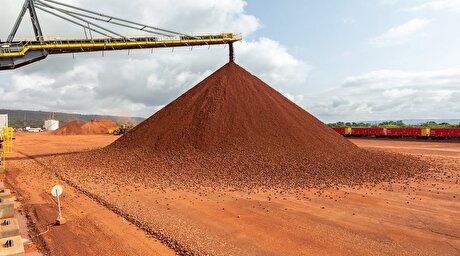
It is possible to convert a bushing from hydrodynamic to hydrostatic while maintaining a constant oil pressure of the load area, thus reducing the friction coefficient between bushing and sleeve (up to 0.001) and increasing the lifetime and efficiency of the bushing.
A complete conversion of the bearing body also entails transforming the sleeve from Full Key (FK) to Semi Keyless (SK). This increases the load-bearing capacity of the bearing, while reducing to a minimum strip defects due to Backup Rolls (BUR) during rolling (-75%), with consequent increase of productivity.
Neither of these modifications require making changes to the existing equipment.
By investing in research, Danieli was able to develop a new Seal End Plate (with all surfaces nitrided), new roll neck seals (Danieli patent) and a new roll-coolant seal (Danieli patent) to retain the oil within the bearing and prevent infiltration of the coolant.
The standard roll-neck seal rotates with the roll and has garter springs and internal stiffening to prevent it from being deformed by centrifugal forces when rotating at high speeds.
For the cold rolling mills, careful selection of the correct grade of rubber combined with PTFE lips has substantially reduced heat hardening of conventional seals, which leads to premature failure.
Nitreg hardening ensures a hard-wearing and heat-conducting seal-running surface that outperforms ceramic coatings.
In the traditional configuration, the backup-roll chock is fastened to the roll body with a threaded locknut assembly.
This threaded assembly requires the use of an overhead crane, pin and wire rope wound around the circumference of the lock nut for tightening and loosening.
This method carries the risk of projectiles due to pin failure and does not indicate how much load is present during fastening or loosening.
One of the latest innovations that Danieli bringing to the market to solve the above-mentioned problems is the mechanical lock referred to as T-lock provides the same results as the hydraulic one while at the same time being less invasive and costly.
The T-lock, in fact, fits the existing backup roll perfectly, ensuring that the sleeves and other components are in the proper operating position, with a measurable locking pressure that is not possible with the traditional method.
At the same time, the use of a cable and crane is eliminated, thus guaranteeing operator safety during the assembly and disassembly operations in the workshop.
— No modification to existing equipment
— Higher load carrying capacity and accuracy
— Greater reduction of the flatness defects (-75%)
— No oil and water leakage into or out of the bearing
— Quicker assembly in the roll shop and improved safety procedures in the roll shop
— Improved service life for bearing components and reduced investment and operational cost