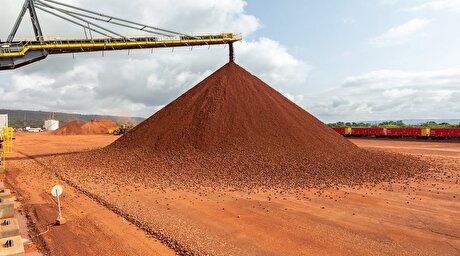
In order to increase the productivity on its Taoyuan bar mill, Tung Ho will install a new K-WELDING line to perform endless welding rolling.
The order for the new line was awarded in August 2016, with startup expected to take place in autumn 2017. With this plant upgrade Tung Ho will be the “first in the country” to operate in endless rolling mode on Rolling Mill #1, which has an average capacity of approximately 600,000 tpy in rebar products starting from 150-mm-square, 12-m-long billets.
Installed at the delivery side of the re-heating furnace, the K-WELDING is an in-line automatic continuous welding system for billets ensuring uninterrupted production of long products.
The process substantially increases productivity, material yield and plant efficiency, while reducing production costs and maintaining homogeneous material quality throughout the whole endlessly-rolled stock.
Danieli’s Endless Rolling of billets features advanced Danieli Automation Level 2 controls, models and setup. The EWR process also constitutes the necessary upgrade to shift production of rebar primarily toward compact coils that - especially in tonnages from 3.5 to 5 t - are recording consistent increases in market demand. In this regard, Danieli offers an unparalleled experience by combining the EWR process with the K-SPOOL, Danieli’s compact coil spooling technology.
The K-WELDINGsystem to be supplied at Taoyuan is the fourth generation of Danieli welding machines since 1997. It will be the first to operate along with an induction furnace.
Tung Ho Steel is one of the most important structural steel producers in Taiwan. Originally known as “Tung Ho Hardware” it began with ship dismantling and selling steel, and in early 1962 it became the first H-beam producer in Taiwan.