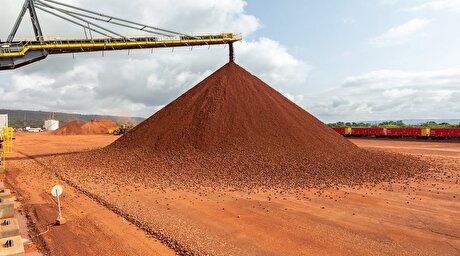
Global warming, geopolitical issues, disruption in the automotive industry: The world keeps changing. Changing markets mean new challenges but also new opportunities. As part of the 27th China Foundry Industry Meeting in Shandong Weifang, Franz Friedrich Butz, president of the HA Group gave a lecture on August 13.
“Innovative Foundry Technologies Support Current Trends in the Automotive Industry”
Energy conservation and emission reduction is the way for China’s automotive industry to go forward. According to the green development targets and requirements proposed in the Mid- and Long-term Development Plan for the Automotive Industry, vehicle manufacturers will be focusing on light-weight production, reduction of fuel consumption and the development of new energy vehicles (NEVs).
This generates new opportunities for the foundry industry, but also some challenges for the future.
Emission reduction as a guiding principle
It is obvious: Due to ever stricter environmental regulations, emission reduction and the improvement of the CO2 footprint over the entire value-stream will remain a main issue in the automotive industry as well as in the foundry industry – not only in China but also worldwide.
To reduce the impact on the environment and improve the environmental behaviour of automobiles as well as of foundry processes, HA offers customers a series of innovative and effective solutions.
Light-weighting can be realised with the help of innovative, high performance binder systems and core making technologies
Example: Structural elements for as example suspension components can be made by aluminium castings with hollow design and increased stiffness-performance. HA inorganic-core binders offer an environmentally friendly technology for employees and society.
Emission reduction or even avoidance in foundries can be achieved with the use of inorganic binder systems.
New energy vehicles (BEV, PHEV, FCEV) ask for new foundry technical solutions; e.g. an efficient thermal management of the electric powertrain requires cores for complex cooling systems
Project-related cooperation: turning complexity into opportunity
“Time to market” has long become a major competitive factor in the foundry industry. In such a demanding field as foundry technology, it is almost impossible for individual companies to drive technological progress on their own. For a single “player” there are simply too many interrelated factors and parameters to make a quantum leap in innovation alone today.
The early collaboration of foundries, industrial equipment manufacturers, consumables suppliers and, if necessary, universities and other institutes in a simultaneous approach makes it possible to shorten the time required for product and process innovations and optimizations. Therefore HA offers the involvement of all parties right from the start – being convinced that working simultaneously on different aspects of a solution leads to better and faster results.
In short: Partnership and simultaneous engineering over the entire value chain make it possible to turn complexity into opportunity.
Lighthouse project: Inorganic core production at an automotive foundry in China
Due to drastic new environmental regulations, a large Chinese automotive foundry was forced to completely convert its core production from organic to inorganic in just one year. In this short time, three production lines with 36 core shooters had to be installed and commissioned. The Chinese foundry had no previous experience with inorganic core production. It involved HA and other suppliers right from the start. Working together, the partners achieved what the individual participants had previously hardly thought possible: The project, unique in its type and size, made rapid progress thanks to the outstanding cooperation between the various stakeholders and was completed successfully within the allotted time.