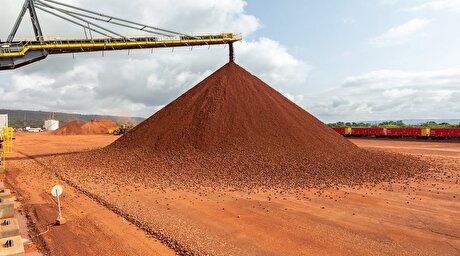
“The reality is that traditional metal recycling methods are not capable of meeting the industry’s demand in terms of quality and volume,” added Alireza Ashraf, noting that the scrap recycling process must be fully “industrialized”, IRNA reported.
The council is a formal institution providing an opportunity to improve interaction and collaborations between the state branches, especially the executive branch and the private sector.
According to Shahram Saber-Tehrani, the head of Khorasan Steel Complex’s research department, scrap metal collecting and sorting are usually done manually in unlicensed scrapyards in Iran.
Utilizing this outdated method keeps the country’s scrap metal supply below the required industrial level. Furthermore, the recyclers forgo the crucial process of separating clean from dirty scraps.
The steelmakers, in turn, feed their mills with low-quality, environmentally unfriendly scraps while struggling with an unbalanced supply and demand chain.
Using dirty scraps in furnaces prolongs the steelmaking process, as more energy and electrodes must be used to burn away the impurities. This will both reduce the output volume and end-product quality.
This is while, according to the industry expert, Iranian industries, especially the auto sector, have high scrap metal production capacity which, if harnessed as per global industrial standards, can enhance the steel industry’s output by cutting production costs and increasing product quality.
“Currently Iran has more than 4 million dilapidated cars, with 350,000-400,000 being added every year, in addition to 30,000 trucks, buses, minibuses and tractors that need to be scrapped. We forecast that about 10 million tons of scrap metal will be made available in the next few years following the lifting of nuclear sanctions and the renovation of domestic industries,” Saber-Tehrani said.
Iranian steel mills need 6 million tons of scrap metal per year to reach the 55-million-ton output target stipulated in the 20-Year National Vision Plan (2005-25).