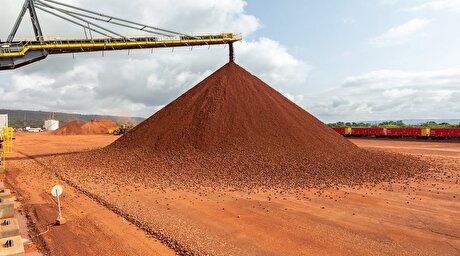
Steel Dynamics Inc. (SDI) has awarded SMS group (www.sms-group.com) an order for the supply of a complete steel production line, from the steelworks to the CSP® plant and from the cold rolling mill to the galvanizing line for its Sinton location in the state of Texas.
With an annual capacity of 3 million short tons (2.7 million tons) of steel the plant's productivity is setting new standards. In addition to the mechanical equipment from the liquid phase up to strip processing, the scope of supply by SMS group comprises X-Pact® electrical and automation systems as well as technical support during installation and commissioning.
Commissioning is scheduled for mid-2021.
For SDI’s production line, the systems supplier SMS group will supply the following components: The steelworks will be equipped with two direct-current electric arc furnaces (DC-EAF) having a capacity of 210 short tons (190 tons) each and two twin ladle furnaces (LF) and a double vacuum tank degasser (VD). It has an annual capacity of liquid steel of over three million tons.
The CSP® plant will enable SDI to produce thin slabs with thicknesses of up to 5.2" (130 millimeters) and slab widths of up to 84" (2,134 millimeters).
The CSP® continuous caster is designed as a single-strand curved mold plant (VLB – Vertical Liquid Bending). With a metallurgical length of over 82ft (25 meters) a yield of 7.5 tons per minute and casting speeds of up to 19.7ft/min (6 meters per minute) are attained.
An eight-stand rolling mill will enable SDI to produce API hot strip grades with thicknesses up to 1" (25.4 millimeters) and widths up to 84" (2,134 millimeters). The mill is designed for a minimal strip thickness of 0.047" (1.2 millimeters).
This CSP® plant will have a hot strip capacity of 3 million short tons (2.7 million tons) per year.
“With this new plant for SDI, SMS group will again make a statement for cost-efficient production paired with higher throughput and better quality,” says Cosimo Cecere, Head of Sales and Project Management CSP® Plants, SMS group.
Following the CSP® plant, a five-stand pickling line/tandem cold mill will be arranged. To meet future demands, the process section of the pickling line/tandem cold mill (PL/TCM) will be equipped with SMS group‘s latest turbulence technology and a 600-kN leveling unit. With the aid of a payoff reel upstream the tandem cold mill, the pickling line and tandem cold mill can be operated in parallel independent of each other. This permits the hot strip to be pickled and oiled or directly guided to the tandem cold mill. The annual pickling capacity will be 1.1 million short tons (1.0 million tons).
The five-stand, six-high tandem cold mill will have a wide roll gap setting range and thus ensure excellent cold strip tolerances and strip flatness. The strip width is 78" (1,981 millimeters). The tandem cold mill will be able to roll the cold strip down to 0.08" (0.20 millimeters).
A carousel reel will finally coil the rolled cold strip. In coupled mode with the continuous pickling line the annual capacity will be 850,000 short tons (0.77 million tons).
The skin-pass mill for post-treatment of hot and cold strip with priority at cold strip skin-passing is designed for an annual capacity of 440,000 short tons (0.4 million tons).
For cold and hot strip galvanizing, the plant will be equipped with a continuous galvanizing line including a horizontal Drever furnace heated by a direct-fired and a radiant-tube zone. The line will be prepared for the later installation of an ultra-fast gas cooling section to allow for future production of high-strength steel. The scope of supply also includes a DUMA-BANDZINK air knife system that will homogeneously and precisely set the zinc layer thickness to ensure high surface quality. A change system with two zinc pots will permit the strips to be coated with a conventional zinc layer or an aluminum-zinc alloy. For post-treatment, the line will be equipped with a four-high skin-pass mill stand, a tension leveler and two horizontal shuttle-roll coaters, as well as with an oiling machine in the exit section. The galvanizing line will be able to process strips with a thickness of up to 0.16" (4 millimeters) and a width up to 76" (1,930 millimeters). Its annual capacity will be 550,000 short tons (0.5 million tons).
For the complete technological part of the new plant complex, the X-Pact® electrical and automation systems included in the supply scope are an important factor. They assure that productivity, production flexibility and quality of the final products will meet actual and future requirements. The applied concept and equipment provide a solid foundation for the digitalization of the plants and processes and for future-oriented extensions and applications. Diagnosis and visualization concepts will be used in the entire plant. They assure and sustain effective and preventive maintenance activities.
SDI intends to sell the products in the rapidly expanding markets of high-strength steel tubes, multi-phase steels for vehicle construction and structural steels for various applications. SDI will become the leader for this new type of minimill for the production of hot strip. In particular, it is the new, extremely high-performance continuous caster in combination with the proven thermo-mechanical rolling process that will allow the production of special steels in unprecedented dimensions.
Mark D. Millett, CEO of Steel Dynamics, Inc., says: “The leading position in technology and the longstanding partnership between SDI and SMS group were the decision-making factors for awarding the order to SMS group.ˮ
Burkhard Dahmen, CEO of SMS group, says: “Steel Dynamics and SMS group have successfully completed numerous highlight projects in the past. In constructing the new plant complex in Sinton, Texas, we continue our fruitful and trusting partnership. The new project will once again illustrate the position of SMS group as Leading Partner in the World of Metals.ˮ
Steel Dynamics, Inc. (SDI), headquartered in Fort Wayne, Indiana, is one of the largest steel producers and metal recyclers in the United States with production facilities located throughout the United States, and in Mexico.
For the new site at Sinton, SDI selected SMS group to supply a complete steel plant complex for the production of special grades. 1) Zwei Gleichstrom-Elektrolichtbogenöfen, zwei Doppel-Pfannenöfen und eine Doppel-Vakuum-Tankentgasungsanlage 2) CSP®-Anlage der neusten Generation 3) Fünfgerüstige Beiz-/Tandemstraße 4) Dressierwalzwerk 5) Verzinkungslinie