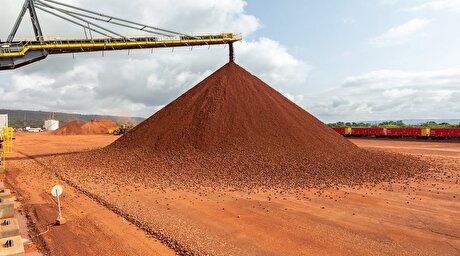
The ARCCESS® electric arc furnace with the patented SIS (SMS Injection System) oxygen injection system.
SMS group has successfully commissioned an electric steel plant with efficient environmental technology and a single-strand continuous slab caster at PT. Gunung in Bekasi (West Java province), Indonesia.
The melt shop with the ARCCESS® electric arc furnace and a ladle furnace is designed for an annual production of 1.2 million tons of steel to be cast into slabs on the new continuous caster.
SMS group supplied the complete basic and detail engineering, the mechanical and electrical core components and the supervision of erection and commissioning. The SMS group scope of supply furthermore includes the complete X-Pact® electrical and automation system including Level 2 automation and commissioning according to the tried and tested "Plug&Work" concept.
B.K. Dutta, General Director: “The new works is of high strategic importance to us. Until now, we had to purchase slabs. By producing slabs ourselves, we do not only achieve a higher creation of value, but also ensure high quality thanks to the plants supplied by SMS group. Of course, all our plants are energy-efficient and easy on the environment. That is why we purchased them from SMS group.” SMS group supplied an 120-ton ARCCESS® electric arc furnace and a 120-ton ladle furnace for the new steelworks complex. The range of charge materials for the electric arc furnace includes scrap, HBI (Hot Briquetted Iron) and hot metal.
Electric arc furnaces of the ARCCESS® series are optimized for highly efficient use of electrical and chemical energy. The electric arc furnace at PT. Gunung is equipped with the latest generation of the patented SIS (SMS Injection System) oxygen injection system, which combines innovative injection and burner technologies. This concept proves its worth through high productivity while keeping production costs low.
SMS group has equipped the electric arc furnace with a gas cleaning system. The dust-laden gases arising at the furnace and ancillary plants during the steelmaking process are efficiently captured and reduced to a residual dust content of less than 10 mg/Nm³. The system is operated by speed-controlled fans which consume a minimum of electrical power as the suction capacity is optimized depending on the specific process.
The continuous caster is designed for the production of slabs with thicknesses of 220 and 250 millimeters and widths from 800 to 2,100 millimeters. The range of grades produced will comprise structural steels as well as pipe and heavy-plate grades.
The segments are equipped with STEC-Roll® technology. Rolls of this technology optimize the casting process and set new standards for cost-effective maintenance and servicing, thanks to their long service life and the possibility of re-using them.
The continuous caster is equipped with modules from the ISC® (Intelligent Slab Casting) package, which ensure optimal plant productivity and slab quality. These modules include the hydraulically actuated resonance oscillation system, the mold with remote-adjustable narrow faces for changing the slab width during casting, as well as the Mold Monitoring System.
The horizontal part of the strand guide system uses position-controlled CyberLink segments. Dynamic Soft Reduction® in combination with the metallurgical process model DSC® (Dynamic Solidification Control) to control secondary cooling allows the production of slabs with perfect internal quality.
On the new plant, PT. Gunung produces high-quality slabs for further processing in its own Steckel and heavy plate mills.
At the Bekasi location, PT. Gunung operates a long-product line for the production of sections and wire rods, as well as a flat-product line for the production of heavy plates and pipes. All major production lines were supplied by the SMS group.
The continuous caster produces high-quality slabs.