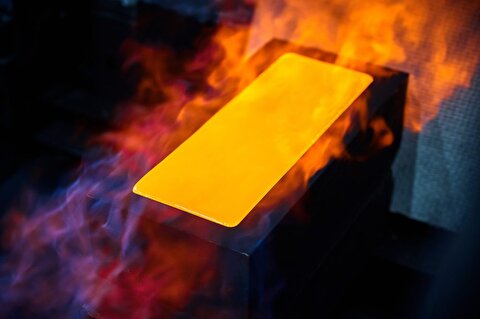
The demand for Metso's in-depth shutdown knowledge and professional services has steadily grown over the past few years. In 2015, Metso was involved in over 100 shutdowns and turnarounds around the world at refineries, petrochemical, natural gas and biofuel plants as well as pulp mills. Customers increasingly count on Metso's service expertise, capability and scope of offering that includes tailored solutions related to shutdowns.
"A shutdown can be considered a strategic project for the plant, a way to manage its resources. Professional planning, efficient execution and on-time startup ensure safety as well as high plant availability and reliability until the next planned shutdown. We are constantly developing our valve service capabilities and service center network to increase our customers' productivity," points out Timo Hänninen, Vice President, Flow Control Services, Metso.
One of the recent major turnarounds in the oil and gas industry in which Metso participated during 2015 took place at Neste's Porvoo refinery in Finland. Metso's service solution for the turnaround consisted of valve maintenance planning, replacement equipment, maintenance and spare parts, as well as real-time project follow-up. In all, about 270 Metso valves were maintained during the shutdown, providing the customer with significant improvements for valve availability.
Efficient shutdown execution and a smooth startup call for a well-planned shutdown scope, actions, materials and resources, and all these are determined through Metso's shutdown solutions. Valve maintenance planning for a turnaround project is always preceded by close cooperation between the customer and Metso. "It is the level of planning that determines the success of shutdown execution," Timo Hänninen says. "Having Metso as a partner for shutdown planning ensures the availability of the correct materials and resources, when needed. It minimizes risks, too."
For example, Metso's preparatory work for the turnaround activities at one of the largest oil refineries in Poland, the GRUPA LOTOS refinery in Gdansk, has been underway for years, although the shutdown will only take place in 2017.
To ensure the plant's safe operation until the next planned shutdown, Metso's experts carefully identify the equipment in need of upgrading, maintenance or replacement. This not only defines the shutdown scope and activities, but also determines the shutdown schedule and the needed resources and materials.
Equipment maintenance is carried out using Metso's original spare parts, maintenance procedures and recommendations to guarantee the same quality, warranty and certification that Metso offers for new products.
In 2015, Metso opened five new valve service centers and today offers flow control services through more than 40 service centers worldwide. The service centers strengthen Metso's position to stage, test and service large numbers of valves to meet customers' high-volume, fast-turnaround repair and service needs during scheduled plant shutdowns. Services are provided for Metso and third-party field devices, including valves, actuators, smart devices and pumps.