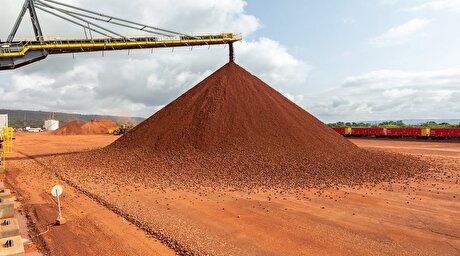
The new complex, which will process 500,000 tpy of cold rolled galvanized and painted material to cover the automotive non-exposed panels, appliances, and construction market requirements, will be installed in Tashkent, Uzbekistan.
The push-pull pickling section -based on Danieli Turboflo technology- combines highly-efficient tank design and process control to ensure the production of iron oxide-free strip over the entire product range and strip speeds.
The two-stand reversing mill which will operate at up to 1,200 mpm features an optimized mill layout configuration and an advanced tuning system for mill threading and tailing out sequences, that will lead to a high material yield.
The hot-dip galvanizing line will produce CQ, DQ, DDQ, and HSLA coated grades with excellent coating uniformity (down to 40 g/m2 each side at 180 mpm) of strip in thicknesses from 0.3 to 1.2 mm and widths from 800 to 1,250 mm.
The 300,000-tpy color-coating line features coaters based on single-slide design that allow specific paint thickness to be applied evenly across the strip surface.
Danieli Automation will supply all the electrical equipment and control systems, including equipment control and process control for the entire complex, providing an integrated and optimized system configuration.
Danieli Service will provide the DMMS suite for effective and efficient preventive maintenance, spare parts, personnel, equipment costs and fault analysis management, according to Industry 4.0.
Turnkey construction will be undertaken by Russian MetProm. The new complex will come on stream gradually in 2019.