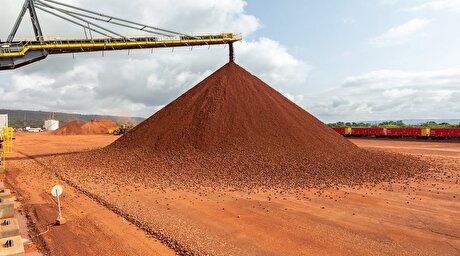
On the first day of the Fourth Danieli Innovation Meeting, following two panel discussions to examine the New Normal metals consumption era and the possibilities for regional and micro and minimills to serve as a model for competitive operations during such a period, the audience of 600 steel and nonferrous metals executives listened attentively to a series of presentations on some of the parallel considerations for strategic planning and investment.
In their presentation, “Green Metal: commitment for a sustainable world,” Gianfranco Marconi and Alberto Zugliano described steelmaking technologies that fulfill the requirements for addressing the global issue of pollution by reducing energy consumption and GHG (greenhouse gas) emissions. By analyzing the energy efficiency of the three main routes of steel production, it is possible to identify the improvements that are possible in each case, to reach the minimum practical value for these reductions. Thus, they concluded:
1. BF and BOF are mature steelmaking technologies, operating now at close to maximum efficiency, with possible improvements only in the auxiliary systems.
2. Scrap and EAF routes to steel production still offer room for real improvements in emissions reduction, and the Danieli proposal centers on the digital Q-MELT package for optimizing the melting process while managing energy consumption.
3. DRP and EAF: the ENERGIRON process is a ‘green solution’ ready now to address steelmaking energy consumption and GHG emissions standards for the future.
Paolo Razza, Sandro Orlando, and Ivan Bosnjak, all of the Danieli Team, detailed “Technological packages to improve plants and processes.” Working from the premise that even as the New Normal period challenges steel industry growth, plant improvement and modernization remain critical to the competitiveness of steelmakers, the presenters noted that such tactics may include equipment upgrades and integrating advanced processes and production methods. The New Normal market prescribes targeted improvements rather than extensive greenfield installations, they explained."
Danieli technology “packages”— defined as Plug & Play or Tailor-made Tech Packages —are devised to reduce conversion costs, enhance product quality, expand product ranges, improve operator safety and environmental sustainability, apply predictive maintenance methods and minimize maintenance procedures, and shorten implementation periods. Danieli is focused on developing and standardizing high-quality technological packages that are proven to be financially and technically feasible to deliver technological, ecological, and economical benefits.
Following this, Marco Ometto of Danieli Automation and Prof. Thomas Parisini of the University of Trieste addressed the emerging, dynamic and digitalized approach to information management, and the Danieli strategy for fulfilling it together with customers. In “Digi&Met: automation for consistency in quality, plant utilization, OpEx and faster deliveries,” they explained how new investments to achieve Industry 4.0 capabilities are a priority for businesses today. The Danieli approach to Industry 4.0 is based on digital innovation as well as on outcome economy principles, to transform conventional plants into Smart Plants.
Some of the results of this approach already indicate the potential of digitalization enabling technologies, including:
• Coordination and optimization of planning, scheduling and logistics processes that are able to achieve One-Day "Production-to-Shipment" Lead Time
• Control of the EAF process using a real-time predictive model, based on a machine learning system that is fed by process data to reduce electrical energy consumption by 25 kWh/t
• Estimation of the steel bath temperature with a 5°C prediction accuracy
• Prediction of material mechanical properties through a machine-learning model fed by process data, to reduce by 25% the need for tested samples
“Endless” production concepts have been in development by Danieli for more than two decades, to maximize input values and increase plant productivity. In “Why endless rolling for long and flat products?” Andrea De Luca and Alessandro Pigani of Danieli, and Wang Guiyang of Shougang Jingtang, profiled two of the most recent breakthroughs for the “endless” approach. First, the MIDA® -Micromill Danieli- plant design for endless production of commodity long products can achieve a rolling mill yield of 99.7%, with a plant utilization factor in excess of 90%. At the same time, the plant OpEx is reduced by 20% on average compared with traditional minimills.
Also, the DUE® -Danieli Universal Endless- package makes possible coil-to-coil and endless production for thermo-mechanical and multi-phase, ultra-thin and thick product, from a single production line. Further, the effective combination of different energy sources makes it a “green” production process, significantly reducing OpEx by 15-20% compared to the current thin slab-based benchmark plants.
Another “endless” achievement described a recent accomplishment for nonferrous production, “Sural, Quebec: the most competitive endless rod mill for the widest range of aluminum series.” Nicola Pontoni and Carmelo Maria Brocato narrated the development of the Danieli rod plant in full operation now, which reflects the most flexible, advanced and efficient technology available to the market for producing a broad range of aluminum alloy rods, both for mechanical and electrical applications. Furthermore, the design was conceived to explore the production of new alloy rod products, not yet commercially available.
The entire endless production process is fully managed by an intelligent control system that supervises the production schedule and plans set-up and quality control for a flexible and repetitive process.
Finally, the package of technical solutions and control adopted makes it possible to establish OEE (Overall Equipment Effectiveness) in the range of 90%.
An important concern for metals industry stakeholders during the New Normal is the scarcity of knowledge and skill to execute advanced technological programs. In “Turnkey projects and product on hand: Global expertise for EPC management and production” Giacomo Mareschi Danieli and Mauro Pitton examined how actual market contingencies enhance the need to fully control the risks associated with the execution of a turnkey (TK) project. Costs associated with plant operations and maintenance over a 20- to 30-year period may run 100 times higher than the costs for design and construction, they noted, thus the “TK business” service proposed by Danieli combines:
- Proper market assessment
- Strategic positioning of the product in the value pools of the market
- Defining the best sustainable solution for CapEx/OpEx optimization
- Executing the plant design and construction
- Endless support, up to business success, in partnership with the plant owner, until production is achieved.
Finally, Gianluca Del Fabbro and Annacristina Mansutti profiled the program of “Danieli worldwide workshops to serve the customers better.” The Danieli Group’s know-how may be found not only in its technological process and design expertise, Del Fabbro explained: it is also proven by the manufacturing capabilities that developed and consolidated over time, always with the aim to offer customers cutting-edge equipment and prompt services. Now, with advanced manufacturing plants in all the most significant steel markets, it is possible to deliver consistent quality results worldwide.
During the New Normal period, the key factors for organizational success may be seen on three broad fronts, they stated: Service and Proximity to Customers, Competitiveness and Capability for Innovation. All these objectives are fulfilled through the Smart Manufacturing model, Lean Thinking and the new Danieli Integrated Industrial Network brand.