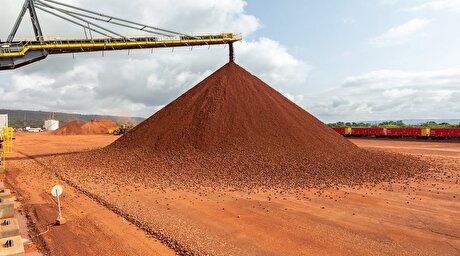
“Ferriere Nord: endless bar spooling by welding benchmark plant,” described the K-Welding and K-Spool packages that represent most innovative developments in billet welding and compact coil spooling technologies. Homogeneous mechanical characteristics, stability in decoiling, cutting and bending processing are the main benefits. The maximum coil weight of 2.5 tons, thanks to the welding process, is now 5 tons, and the next steps toward 8-ton coils are being taken now.
“H3 wirerod mills: high-productivity, high-efficiency, high-quality,” considered how increasing demand for SBQ wirerod is challenging producers to enhance technologies by combining high plant productivity and efficiency with process flexibility. The possibility of changing the process route according to the final application of the wire rod and to simplify production planning represent the key to success. The Danieli H3 vision combines proven technology, automation control and experience with strong, long-lasting relationships between steel producers and machinery suppliers.
“Superior wirerod finishing and handling systems over the decades,” traced the development of the Sund Birsta coil handling system, compactors, wire and strapping machines, for handling wire rod coils and bar bundles in an intelligent and safe way, while reducing operational and maintenance costs. The latest technology advancements concern electrifying the SUNDCO coil handling system, the Sirius coil compactor and KNDelta wire binding, further emphasizing best-in-class energy efficiency and superior performance. The breakthrough development of the SBHLW strapping unit with laser technology will change the role of the steel strap material that will benefit the end user by significantly reducing the overall and operational costs.
“The Drawer: 4-roll drawing/sizing mill for best accuracy and internal quality,” examined how to maximize the value of hot-rolled steel bars for most mechanical applications. Prime quality product means fewer problems downstream, minimized recovery activities and higher margin for the end-user, up to +15%. Robust automation sets a new standard in quality and provides consistent dimensions on the final bar, regardless the variability of the upstream process. Fully automated production and workshop minimize stoppages and avoid set-up mistakes, increasing the output of the plant up to +10%.
“RollX: taking bar rolling into a new dimension,” is a review of the new on-line guiding concept, the patented RollX roller guides, that optimizes production by providing greater flexibility, overall efficiency, quality control and safety through a new approach and the use of an on-line, remote-controlled roller guide with servo motor force controls. Service intervals are increased up to three times thanks to 75-80% reduction in the roller forces. Mill set-up time is reduced to seconds, and there is no need of the operator’s intervention with hot material.
“Green reheating solutions for sustainable steel production” examined how a new generation of Danieli Centro Combustion furnaces utilizes best combustion technology to improve the design of both process and environmental effects. The focus on staged/flameless burner innovation provides customers with leading-edge technology, allowing higher product quality, lower operating costs, trouble-free operation and increasing environmental friendliness. Danieli Automation Level 2 is a reliable control system to maximize reheating furnaces’ potential, assuring a uniform operation, process cost saving and product quality. It also can lead to the product flow optimization and to improve performance of the entire plant.
“Advanced batch and continuous furnaces for bar and wirerod coil treatment” studied how the steel Industry scenario has changed completely in the past decade, now emphasizing “high-quality final products” (to compete in an over-supplied market), ”efficiency" (to minimize OpEx), and “minimum pollutant emissions”. Danieli Olivotto Ferrè invested in R&D to achieve new targets and satisfy customer needs: tested, reliable, ultra-high efficiency “combustion technologies” have been introduced, successfully applied and are the basis of new heat-treatment plants able to answer the new needs.
“Competitive premium quality section and rail production” revealed how Danieli developed processes and technologies for medium and heavy sections (PSP, QST) and high-strength rails (RH2), including full control of product dimensions and surface defects (HiPROFILE) to achieve premium products with a competitive OpEx.
- The PSP finish rolling process makes it possible to achieve 25% longer campaigns.
- High-yield strength, toughness and weldability with limited addition of alloys (10% less) are possible with QST.
- With the RH2 system it’s possible to increase the rail-head hardness up to 400HB.
- HiPROFILE is used to set the roll gaps on finishing stands through a closed-loop regulation, to achieve consistent dimensional tolerances and to detect surface defects.
“Added-value quench, self-tempering for beams and head-hardening for rails” considered how the markets’ requirements for ever-more demanding sections has been the driving force in the development of new steel grades. Together with alloying design, process lines play a fundamental role. Danieli is focusing its efforts to develop in-line heat treatments for production of superior quality sections:
- Danieli Rail Head Hardening RH2 to treat up to 120 m long rails reaching hardness levels of more than 400 HB on the rail head.
- Danieli Quenching & Self Tempering enables the production of fine-grain, high-strength structural steel up to grade 70, with a potential reduction of 20% in the material cost of buildings.
“Megagrinder and Intelligrind for defect-free flat and long products” address the necessity for conditioning flat and long semi-finished products before rolling — not only in “traditional” fields of stainless and alloy steels, but also, for specific sectors, in low- and medium-carbon grades. Danieli pioneered grinding in large volumes 15 years ago with the introduction of the 630-kW Supergrinders, and now innovative technologies based on three-dimensional surface defect detection have been developed. The new, 1000-kW MegaGrinder serves plants for inspection and conditioning of low- and medium-carbon grades in large volume up to 1 million tons/year, based on economical and environment-friendly technologies and applications.
“Smart maintenance: a flexible cost-effective tool for improved plant reliability,” considered how the basic principle of the Fourth Industrial Revolution is that communication and the symbiosis of individual, specialized components work effectively to achieve a greater overall result. Danieli is addressing the concept of smart maintenance, where equipment is born or can be retrofitted with devices that make it ready to interact in the smart factory environment. Flexibility, openness and the use of best-in-class technologies are the driving forces of Danieli Digi&Met Smart Maintenance, which is one of the digital-enabling technologies for the smart factory.