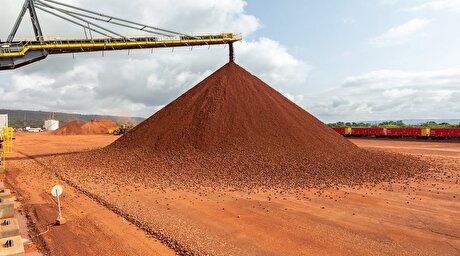
Guests who attended the flat products session at the Fourth Danieli Innovaction Meeting learned of several recent developments and successful operations, including:
“Customer relationship: a reliable partnership program after plant commissioning” described the ways that Danieli strengthens its relations with customers through plants in operation. With the start of the CRP program in 2016, multiple technological topics have been commonly identified and investigated according to customers’ priorities, so that experts of both parties may work together on these subjects to meet new market demands, to create innovative solutions and to master future challenges. All topics can be clustered in categories such as: quality improvement, stable steel production, OpEx optimization, future market requirements, digitization, and Big Data analytics.
“QSP thin slab technology and Danieli Universal Endless” traced the development of this thin slab casting and rolling process, beginning more than 25 years ago, and described how today's customers’ requirements for higher levels of quality and flexibility are addressed by the latest generation QSP technology. Danieli’s vertical-curved thin slab casting technology is at the core of a more advanced plant concept. Productivity per casting strand ranges from 0.7 to 2.5 MTPY and can be increased in steps (an ‘evolutionary’ concept.) The HSM has separate roughing and finishing mill groups, so additional equipment may be installed in the transfer bar area to widen the product portfolio. This will optimize and customize the plant concept to fulfill all customer requirements.
“Old beauties shine again: how yesterday’s hot-strip mills can be competitive again” was a discussion of the modernization concepts available to raise older hot-strip mills to the same level of technical capability as state-of-the-art hot-strip mills. Customized revamping concepts are developed as integrated solutions for design, manufacturing, electrical and automation systems, incorporating our own process know how.
In cooperation with customers these technical solutions have been successful at increasing HSM production capacity by 14%; increasing incoming slab thickness by 11%; reducing the width tolerance from 0/+15mm to 0/+5mm; and increasing the rolling torque by 50%.
“Modern plate/Steckel mills: the highest levels of flexibility and competitiveness” referenced the successful installation for wide product rolling at Chinalco, as well as a new project for Midhani. Mini and modern plate mills and Steckel mills support production rates as low as 50,000 to 70,000 t/y, with high quality (e.g., thickness tolerances less than 30 micron) and within a sustainable CapEx requirements. Danieli Automation integrates the plants with advanced control tools meant to boost yield (by up to 2%), quality, shape and compliance to mechanical properties. While seeking to improve efficiency, JSW Steel Texas introduces a vision for the plate mill of the future and its successful cooperation with Danieli.
“Hot-strip production 4.0: advanced automation for highest production savings” connected the needs of flat product rolling to the digitalization megatrend shaping the future of industrial operation. For steel plants this trend started many years ago and today it is normal to optimize the production using big data analytics and integrated quality and process systems. Nevertheless, Danieli keeps developing innovative Industry 4.0 solutions and smart sensors in order to further increase process control, process know-how and intelligent predictive maintenance to reduce OpEx, save energy, reduce environmental issues, and increase safety for plant operations. Danieli`s portfolio of technological packages provides the latest, future-oriented measurement and tracking systems, and it is expanding to include new capabilities for digitalization.
“A success story in Mubea: build a successful partnership and grow together” related the details of collaboration by Muhr and Bender KG (Mubea), Germany, and Danieli that started from a common development of a special flex rolling mill and expanded to large-scale production under exclusive technological cooperation. Mubea is a global market leader in development and manufacturing of automobile products and a lightweight component design specialist, and it is the leading producer tailor rolled blanks.
“HiPAC: high-performance automation and control automation platform” offered a profile of this process control platform with a lean, powerful, open, and modular system architecture that converts commercial, off-the-shelf hardware into a powerful Industry 4.0 controller. HiPAC controls flat, long / tube mills, and for drives, induction heating and EAF arc estimation, with more than 600 installations during 2014-2015. Recently HiPAC was chosen by AM Gent for its HSM L1 upgrade due to its well-designed, multi-functional, flexible and proven controls and interfaces. The choice was confirmed by completion of an overall upgrade process, with improved quality and without production losses.
“Yildiz Entegre cold mill complex: the first step of Yildizlar Holding in the steel business” is a report of how the Turkish Yildiz Demir Çelik decided to enter the steel business (it is part of Yildizlar Holding, with more than 100 years’ experience in forestry products, fertilizers, chemistry, port operations, energy generation, and insurance), and how they selected Danieli as supplier of the cold mill complex to be built in Kocaeli. The new complex will process incoming hot-rolled coils for up to 1.5 Mtpy of pickled, cold-rolled, galvanized, and annealed/skin-passed coils for high quality applications.
“Flexible and productive cold mill complexes made simple” summarized the capabilities of Danieli Wean United, the cold rolling mills and strip processing lines division of Danieli, which always works in partnership with customers, emphasizing cooperation, coordination, and innovation. DWU designs, builds and starts new, state-of-the-art, and optimized for CapEx and OpEx cold mill complexes to produce high-quality steel coils. In addition, the Fata Hunter, Olivotto Ferrè, Fröhling, Centro Combustion and Danieli Automation businesses work together as one with DWU to provide 100% in-house technology for cold mill complexes. This provides customers with a single technology source for all pickling, cold rolling, annealing, surface coating, tempering and coil finishing processes.
“Cold mills and strip processing lines: new solutions enhancing competitiveness” described yield-boosting technology in CR that improves product yield up to 1.6% of annual production. CRM PLUS Technology in a cold rolling mill boosts product yield up to 99.4%, and increases production at the same time by approximately 14%.
For coating lines, new developments in the zinc pot area increase the wiping capacity, improve coating uniformity, reduce uniform coating weight and increase the process speed, all leading to higher productivity. Installation of robotic systems provide significant zinc savings due to an optimized and repeatable zinc dross-skimming. The ROI for this application is typically less than one year.