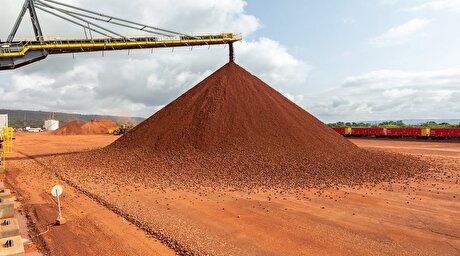
Danieli Innovaction Meeting 2017 opened today at the Group’s headquarters in Italy, drawing 600 guests from 70 countries for a schedule of panel discussion and technology presentations, all arranged to offer Ideas for the New Normal metals consumption period. That theme has defined the current state of steel production in recent years, and the DIM2017 event will present different perspectives on the trends and technologies that will shape the industry’s future.
The first discussion panel of the day addressed directly the New Normal, as World Steel Assn. General Director Edwin Basson narrated the history of steel consumption and industry expansion over the past seven decades. Panelist Emanuele Morandi, CEO of Made in Steel, Italy, declared that advanced controls and automation will define the future of steelmaking operations, predicting that “the factory of the future will produce data, as well as steel.”
Deacero S.A. CEO Raul Gutierrez introduced the opinion that steel demand in regional economies, such as in Mexico, will perform better than the forecast 1.1% expansion through 2035.
CMC Steel CEO Barbara Smith advised the audience that the steel industry must continue to refine and develop scrap processing and recycling, in order to control its raw material costs, and move more production away from the BF/BOF route to the EAF route.
Mark Lin, Chairman and President of Feng Hsing Steel, Taiwan, described the necessity of investing to improve the performance of his company’s operations. This included the original Feng Hsing plant, still profitable and producing 384 different steel products in 240 different dimensions can be produced in a monthly rolling schedule, with a maximum of 70,000 tons/month. A second bar mill, now over 30 years old, is being made more competitive, with the introduction of Danieli technology to roll low-alloy steel at a lower of temperature of 900 °C.
Mr. Lin declared Feng Hsing Steel is becoming the price and production leader for steel profiles in Taiwan, thanks to highly flexible rolling capabilities, supplied by Danieli. “My experience is it very important for a plant to adopt advanced technology, hire talented staff and workers, and make certain to maintain safe production practices. These are the only ways by which the plant can be competitive and the product can be qualified.”
Li Xinchuang, President and Chief Engineer of the China Metallurgical Industry Planning and Research Institute, explained the necessity to plan with careful understanding of population growth and technology trends, making it difficult to forecast demand with reliable accuracy. Of the steel industry’s technology planning, he noted that difficulty for steelmakers to increase or decrease production volumes quickly, adding to the unreliability of production forecasts.
Danieli Chairman Gianpietro Benedetti told the audience that the New Normal compels steel plant and equipment builders to change their operating strategies and product portfolios to address the different needs of steel producers during a period of dynamic changes directed by new technologies.
In addition to decreased steel consumption, Benedetti added that “digitalization will promote smaller production quantities, faster deliveries, and greater flexibility.”
A further highlight of the DIM2017 first day was a second panel discussion on the evolution of the regional micro and minimill model as a strategy for managing the New Normal conditions. World Steel Dynamics Managing Partner Peter F. Marcus presented a colorful analysis of the business, technological, and sociological trends shaping the steel economy today. Among these, he predicted a continued decline in the competitiveness of blast furnace-based iron and steel production, and turmoil in production planning as producers try to manage shorter business cycles with wider shifts in supply and demand of finished products. He described the current period as an “age of discontinuity” in which managers will require skill, patience, and humor to survive.
Marcus was joined on the panel by Giacomo Mareschi Danieli, CEO, Danieli Group, Italy, who traced the development of minimill operations in the global steel industry. He explained how the minimills’ successful strategies in past business cycles – including maintaining competitive CapEx and OpEx, fulfilling regional demand for commodity grades, and adopting new and revolutionary technologies — all remain relevant strategies in the New Normal. In particular, Mr. Danieli cited MicroMill Danieli (MI.DA) concept as a new model for embracing proven management principles.
Horst Wiesinger, of Horst Wiesinger Consulting GmbH, Austria, cited numerous long-term trends in population, raw materials and scrap supply, to explain the strength of the minimill production model versus BF/BOF steelmaking. The minimills remain economically viable because of their flexibility in production volumes, the quality and variety of products, and the high rates of asset utilization. He also noted that minimills show capabilities for become even more competitive in terms of production process time and energy requirements.
Necdet Utkanlar, Board Member, Kroman Çelik Sanayi, Turkey, offered the perspective that rising volumes of scrap worldwide represents an advantage for minimills. Likewise, the emerging possibility of CO2 emissions regulation will benefit minimills in contrast to BF/BOF producers. Further, Mr. Utkanlar predicted that minimills’ flexibility to produce multiple different grades of steel allows them the possibility to shift production programs to address regional market needs.
Alihussain Akberali, Managing Director, BSRM, Bangladesh, offered the perspective that emerging markets need minimill operations to fulfill their potential for economic development. The minimills’ CapEx and OpEx efficiency offer the best opportunity for expansion in regional markets, where working close to the customers’ changing demands is a requirement.
Toshikazu Nishimoto, President, Tokyo Steel, Japan, argued that by 2050 we expect to accumulate 55 billion tons of steel which will generate 1.5 billion tons of scrap metal; this means that 70% of steel demand can be covered by recycled steel product. Technology development will become more and more important in order to produce high-quality finished products using even low-quality scrap. Tokyo Steel succeeded in running its operations by not relying only on high-quality scrap, even to make high-quality flat products. He believes the EAF will play an important role in achieving a low carbon footprint and a recycling-based society, taking the place of the BOF.
At last, Danieli Group Chairman Gianpietro Benedetti described the minimill concept as the hope for steel industry growth and technological development, with the regional expansion offsetting global consumption forecasts. Benedetti further predicted that the Chinese industry would progressively incorporate more minimill operations, to manage costs, increase production flexibility, and resolve the excess of CO2 emissions characteristic of BF/BOF steelmaking.
The first day of DIM2017 also included presentations on Green Metal concepts, and a detailed presentation on the new Danieli Digi&Met strategy to “simplify metals complexity” by embracing Industry 4.0 capabilities and practices.
The Danieli Innovaction Meeting 2017 will continue through Thursday, 5 October, with further discussions of trends in specific product markets, and presentations of new technologies for iron and steelmaking, flat and long products, aluminum and non-ferrous metals, tube, pipe, forging and extrusion, and automation.