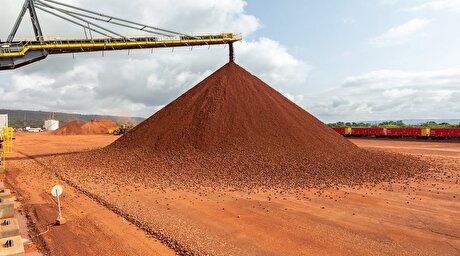
Both systems, MIDREX and PERED, are based on the use of natural gas for the reduction of iron from iron ore pellets.
So far, most of the steel producing plants in Iran, not including Esfahan Steel Company (ESCO) applying blast furnace system, are utilizing MIDREX. Yet, gradually PERED was adopted as well, and steel producing projects including Neyriz, Fars, and Baft, Kerman, are to apply PERED technology. The plans are waiting to be launched in the near future.
The most important features of the technology, as well as the achievements of Mines and Metals Engineering Company (MME) are as follows:
PERED
Persian Direct Reduction Technology
MME GmbH is established and registered in Dusseldorf, Germany since 1996 to provide consultancy, engineering services, and supply for mining and metal industries worldwide.
MME GmbH staff is by senior experts from steel industries with long time experience in the iron and steel making plants and specialized in the design, engineering, and supply.
PERED (Persian Reduction) is a Direct Reduction Technology invented and patented by MME (Mines and Metals Engineering GmbH). It is an economical, energy and raw material flexible technology for producing direct reduced iron.Although various technologies are in existence for producing high metalized DRI, PERED technology for producing DRI is an improved energy efficient with flexibility to work with the different raw material and different energy sources, at reduced overall cost.
PERED DRI PROJECTS of MME
1-SHADEGAN PERED® (0.8 MTPY) TURN KEY
2-MIYANEH PERED® (0.8 MTPY) ENGINEERING & EQUIPMENT SUPPLY
3-NEYIRIZ PERED® (0.8 MTPY) ENGINEERING & EQUIPMENT SUPPLY
4- BAFT PERED® (0.8 MTPY) TURN KEY
5-CSTM PERED® (0.3 MTPY) ENGINEERING & EQUIPMENT SUPPLY WITH SYN GAS
FROM COKE OVEN – P.R. OF CHINA
PERED process consists of several improvements over existing technology
1-Shaft Furnace
Dual reducing gas injection:
Better utilization of the bustle gas by two ducts
Improved distribution of gas in the furnace
Oxide feeding & distribution:
Improved iron oxide distribution inside the furnace by the invention of new feed pipes
Dual top gas off-take design:
Improved to achieve better results
2-Burden Feeders
Changing numbers and arrangement of burden feeders to prevent clustering
3-Cooling Zone
The invention of cooling gas collector and distribution cone:
Injection of cooling gas to cone from outside header
Better collection of cooling gas from cooling area
4-Reformer
10 inch reformer tubes:
Less space requirement
“PERFORMEX” catalyst specially developed
5-Heat Recovery Unit
Inverted bundle design
Less space requirement due to compact design
6- Compressors
Operation with higher pressure by a proved system
Increases the production or reduces power
consumption for the same production
7- Steam Generation
Increasing the reformer efficiency
8- Scrubbers
The most advanced method of gas cleaning:
Less pressure drop and higher efficiency
PERED® technology brings following advantages
Lower capital investment
Lower energy & operation costs
Lower environment pollution
Option for CDRI / HBI/ HDRI
Flexibility to use high Sulphur ore
MME GmbH provides consultancy and support, as well as development in all the phases of projects from feasibility study and its application to the design and engineering by means of project management and consulting service up to supervision of erection and commissioning.
MME GmbH can provide considerable support in the maintenance & spare part management, training, technical assistance and commercial contracting.