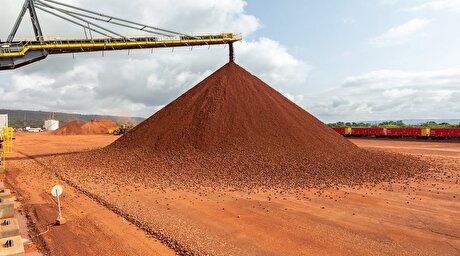
The VCC® (Vertical Compact Coiler) line, which SMS group supplied to ArcelorMittal Zenica d.o.o., Bosnia and Herzegovina, has successfully passed its performance tests. The new line has been designed to produce compact coils at an hourly throughput of 60 tons.
The VCC® line features state-of-the art spooling technology. It spools the rolling stock inline into compact coils. Nowadays, processors require stable, compact and easy-to-process coils. This means that many conventional plants with wire rod blocks and laying heads are more and more often required to recoil their hot rolled coils into compact coils. With the new VCC® line, ArcelorMittal Zenica d.o.o. can now produce compact coils directly inline in a fully automatic process, which minimizes human supervisory work during production. This saves time and HR costs.
The new VCC® line (Vertical Compact Coiler) at ArcelorMittal Zenica d.o.o., Bosnia and Herzegovina, which operates at a throughput of 60 tons per hour.
The mechanical properties are carefully controlled by a set of soft cooling boxes. This not only permits fine tuning of the properties along the entire bar length, but also an immediate switch from the straight to the spooling line. Thanks to this system, each individual coil could be produced in a fast and smooth manner.
The vertical spooling technology developed by SMS group has additional advantages over horizontal designs: the equipment is simpler, easier to install and requires less maintenance. Also the installation effort, including conversion work, is lower.
“We are proud of the successful startup of this new line in the Zenica bar mill,” stated dr. Mustafa Imamovic, Director of Project and Capex department at ArcelorMittal Zenica d.o.o. “It is a very important investment which will increase our competitiveness throughout the European market.”
The project was implemented by SMS group S.p.A. in cooperation with ArcelorMittal Zenica d.o.o. While SMS group took care of the equipment supply and installation, ArcelorMittal Zenica d.o.o. was responsible for the civil works.
The smooth interaction between the existing and the newly supplied equipment proved to be an important key to the success of this project, which was completed within the timeframe of one and a half years specified by the customer.