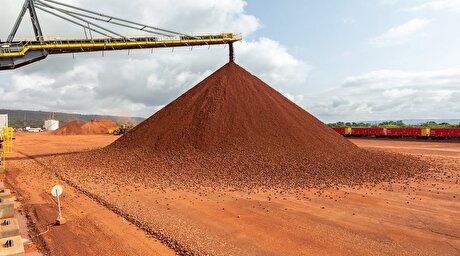
With the new press, the company will be able to further optimize crimping geometries and reduce set-up times. The entire crimping cycle – performed in combination with the associated auxiliary equipment – has been reduced to just 17 seconds.
Crimping is a process that forms metal plate into a dish without reducing the thickness of the plate.
Thanks to the modern hydraulics and control systems, and the three-way-controlled hydraulic cylinders, the new crimping press in operation at voestalpine Tubulars carries out the crimping centrically at very short cycle times. During this process, no shear stress is being induced into the material and there is no buckle formation in between the crimping dies. This will result in a substantial improvement in the crimping shapes of the wide range of very different hollow geometries.
“SMS group has met our expectations in all respects in terms of technology, delivery deadlines, quality and solution competence. The new crimping press will largely improve the plant performance of our push bench area,” says Heinz Teuschl, Head of Operations at the Kindberg mill.
The new crimping press is part of the CPE (Cross Piercing Elongating) line on which voestalpine Tubulars manufactures high-grade tubular products for a broad application range.