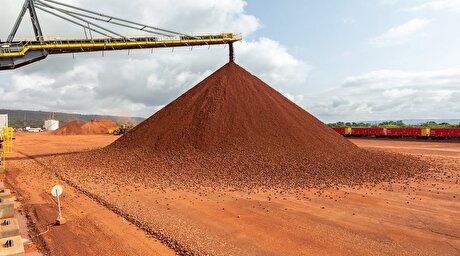
To extract the REE, the scientists dissolve the magnets in nitric acid, and continuously feed the solution through a module supporting polymer membranes. The membranes contain porous hollow fibers with an extractant that serves as a chemical “traffic cop” of sorts, as it creates a selective barrier and lets only rare earth elements pass through. The rare-earth-rich solution collected on the other side is further processed to yield rare earth oxides at purities exceeding 99.5%.
Typically, 70% of a permanent magnet is iron, which is not a rare earth element. However, with the new process, it is possible to completely eliminate Fe components and recover only rare earths. This means that less waste is created when compared to other mechanisms aimed at producing similar results.
“We have developed an energy-efficient, cost-effective, environmentally friendly process to recover high-value critical materials,” said co-inventor Ramesh Bhave of the Oak Ridge National Laboratory, in a media statement. “It’s an improvement over traditional processes, which require facilities with a large footprint, high capital and operating costs and a large amount of waste generated.”
Besides hard drives, magnets are being recovered from magnetic resonance imaging machines, cell phones and hybrid cars. Most of the rare earth elements obtained from them are lanthanides, elements with atomic numbers between 57 and 71 in the periodic table. Examples of these are neodymium, praseodymium and dysprosium.
On its second phase, the program will also explore if the underlying process for separating rare earths can be developed for separating other in-demand elements from lithium-ion batteries, such as lithium and cobalt.