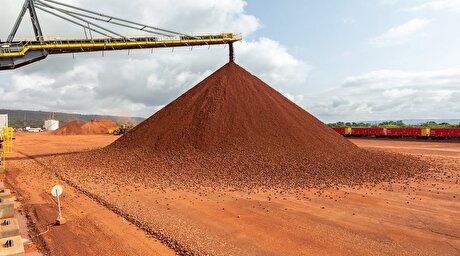
A good quality wax is a key component of the final casting and can reduce rework. This article we will look at some of the waxes that REMET offer to help achieve these process improvements and other green benefits.
A modern foundry needs to consider the environmental impact of their processes as well as the economic drivers of business. With tighter and tighter environmental controls in Europe, America and across the world, and finite global resources, it is more important than ever to have the right product. With this in mind, REMET’s Research & Development Team have developed a range of products that can not only improve your investment casting process but can also reduce your environmental impact. These innovative products have been developed to enhance each stage of the investment casting process and reducing cycle times, without adversely impacting product performance.
The first product that can help you reduce your impact is FF>>Form®. This unique pattern wax contains little or no filler but performs like a highly filled wax. FF>>Form is a wax that has a low freezing range and will “set-up” quickly and is capable of being injected at cooler temperatures than traditional waxes, this can help reduce cycle times by up to 50%.
The formulation of FF>>Form waxes has been fine-tuned to control shrinkage rates dependent on the foundries requirements, this adjustment has no negative effect on the performance of the wax. It is extremely stable and offers excellent dimensional pattern stability even up to two weeks after injecting. FF>>Form is very chemically stable and can tolerate a wide variation in temperatures and pressure during the injection stage, without impacting the final casting.
The proprietary, patented, and complex blend of raw materials means that the wax performs as well as a high-filled wax. The blend can reduce production cycle times, and allows for a reduction in dwell times which leads to increased productivity and throughput.
Minimal, and frequently no, filler in the wax means that the wax can be injected at low temperatures whilst promoting excellent flow characteristics through low viscosity. The low congealing point, without reducing the melting point, allows a faster set-up time, increasing throughput while maintaining the dimensional requirements of highly filled waxes. With minimal filler content, FF>>Form’s formulation also allows for an increased wax reclaim yield with minimal filler residue.
FF>>Form performs best at low temperatures, which causes less internal stress when cooling and provides a number of additional benefits. These include a superior surface finish, less flow variation and reduced flow lines, air traps and non-fill. The wax has a better consistency in paste form requiring less equilibration time and faster shell evacuation during the autoclave cycle.
Key environmental benefits of FF>>Form:
Reduced Energy Waste – By reducing cycle and dwell times of pattern production, combined with the ability to operate your presses at lower temperatures means that the energy required to produce each pattern is reduced.
Reduced Waste During Reclamation – Due to the unique formulation of FF>>Form it has a high reclaim yield, resulting in a reduction of waste from the process.
Minimal Filler Waste – As FF>>Form is a wax that contains low amounts or no filler, depending on the blend, there is little or no filler material being released into the waste stream. Filler in the form of micronized plastics have recently gained much publicity in terms of low-level contamination in the environment. The removal of the need for filler and hence micronized plastics is, therefore, a major step toward improving emissions to the environment.
You can see FF>>Form in action in a case study HERE.
When it comes to reducing filler waste REMET also offers a range of water filled waxes. The Aquacast™ range of waxes are suitable for any size of casting, even large castings, without contraction issues.
The water filling gives the Aquacast range of waxes an excellent surface finish with a glassy smooth appearance. The water reduces the surface defects such as sinkage and cavitation, due to specific heat and density properties.
In addition to this, all materials in the Aquacast range flow well, making these waxes suitable for complex dye geometry. This is complemented by the behavior of the water filling in this material, when in the die, as it allows the wax to release from the die easier. The wax pattern formed from Aquacast waxes still maintains excellent dimensional stability.
Key environmental benefits of Aquacast:
No Filler Waste – As a water-filled wax there is no filler to enter the waste stream
Reduced Waste During Reclamation – Due to the water base of the filler Aquacast is easier to reclaim and offers higher reclaim yields than other filled waxes.
REMET’s team of experienced engineers and technical team will be on hand to help you to get the most out of the waxes and tailor it to your foundry’s specific needs. Talk to your local REMET Territory Manager to discuss how REMET can help you improve your process.
You can see more information on how we are helping foundries to be greener, on our website.
The products highlighted in this article is only a selection of the products that REMET has developed to help reduce the environmental impact of foundries. We are continually developing new and innovative products to improve your process and benefit the environment. Look out for the green badge on our products.