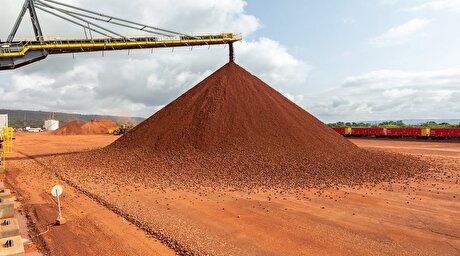
A small machine component winning a design award is probably a first in the history of the German Design Award and certainly worth noting. The component for which plant and mechanical engineering company SMS group has received the German Design Award 2019 in the category “Industry” is a spray head used to cool dies in forging presses. All involved in the various teams that have been working towards the common goal of adopting an entirely new approach to designing and producing a machine component were excited about the news. Not only the component as such was relevant for the judges, but also the fact that it exemplifies the various aspects of Additive Manufacturing, a technology that has been opening a whole range of new possibilities for the design and functional layout of components. Every year the German Design Council organizes the German Design Award, one of the most recognized design awards worldwide. This Award recognizes innovative products and projects, and the companies or individuals who have fabricated and designed them.
Axel Roßbach: Research and Development Extrusion and Forging Presses, SMS group GmbH: “Winning the Design Award makes us extremely proud. It is recognition of many teams within SMS group whose work is characterized by a highly interdisciplinary approach. The spray head is a milestone innovation marking a new era in the design of plant and machine components, enabled by the game-changing potential of 3D printing and function-optimized design. The design of a machine part is today no longer limited by the constraints imposed by conventional – process-optimized – forming and machining techniques. Supported by latest software and computer technology, we can now give a component exactly the design that fulfils its designated function in the best possible way. Another important aspect is that we have used new materials. Therefore the Award honors not only a new design, but above all the new way of thinking lived within SMS group, which has materialized in a global approach to Additive Manufacturing.” According to Axel Roßbach, the new spray head is an example of how nowadays, in the digital age, different disciplines interact and what opportunities Additive Manufacturing holds in store. The new spray head solution produced by 3D printing is the result of a joint effort by the Forging Plants Department, the Additive Manufacturing Project Team and the simulation technology experts of SMS group.
Common spray heads are heavy and complicated to produce. Their heavy weight impairs the productivity of the forging press. Against this, the new spray head has been designed with a view to how it can fulfill its function in the most efficient way. It is significantly smaller, features flow optimized channels and cools the dies specifically and as required in each individual case. Die areas subjected to intensive heating are cooled at a correspondingly – precisely calculated – higher rate than areas less hot. Additionally, these spray heads can be produced virtually just in time. Axel Roßbach: “Although the spray head is only a small component, it nevertheless ideally represents the potential of Additive Manufacturing. The innovative manufacturing methods enabled by 3D printing form the basis for Industrie 4.0. The example of the 3D-printed spray head makes this clear and measurable. Made of plastics, it weighs only one tenth of what a conventional one would weigh. A 3D spray head made of metal weighs up to 70 percent less. It is less expensive, more efficient and can be easily customized and instantly produced. “
All this provides numerous advantages for drop forging operations. Drop forging presses are being constantly optimized with a view to achieving shortest cycle times and maximized service life of the dies. Spray heads for cooling and lubricating the dies perform a key function in the forging process as without them the dies would not be able to withstand the constant and extremely high stress acting on them during operation. The spray heads are introduced between the open dies awaiting the next forging stroke. The innovative SMS group solution means not only a reduction in weight and costs, but also reduced wear of the supporting arms which introduce the spray heads between the dies. Due to the significantly lower mass to be accelerated, cycle times of the - usually automated - processes can be shortened. Another key advantage for the press operator is the possibility of producing customized spray heads “on demand”, i.e. the spare heads are available in virtually no time, without incurring the high costs of keeping them physically in stock. Also the environment benefits as the production of the spray heads consumes no more material than absolutely necessary. SMS group plans to also print current-conducting elements and sensors into the spray heads. This will make it possible to actuate the valves electrically and generate condition messages of the systems. The thus gained added value and the potential for process optimization make the 3D-printed spraying system for drop forging operations a technology ready for Industrie 4.0. Robert Banse, a member of the R & D Project Team SMS group: “We are in no way restricted by any manufacturing constraints. Therefore we can adopt a creative technological approach to designing and start out from the function the component is going to perform. In other words: We develop the perfect design for the function at hand ready, knowing that it can be produced in the 3D printer.”
One of the first customers using the new spray head in practice is Bharat Forge in Ennepetal, Germany. For Bharat Forge, the spray head was specifically designed to allow switching between water and a graphite-based spraying fluid. Both the forge operator and SMS group are extremely satisfied with the performance of the spray head. Bharat Forge: “The spraying pattern is much more homogeneous now. The dies are cleaner. Consequently the overall consumption of spraying fluid has decreased. Also handling is easier than with the conventionally manufactured spray heads. Accumulations of material, as frequently occurring inside the former spray heads, have not been found thanks to the flow-optimized design of the fluid channels.“
Although the Design Award-winning spray head is in the focus of attention above all due to its extraordinary design, this is only one facet of the many activities underway at SMS group in the area of Additive Manufacturing. As the “Leading Partner in the World of Metals”, the company’s plans and strategies are of much wider scope. SMS group is not going to limit its AM activities to the design and production of innovative machine components, but will also offer integrated solutions for the complete process chain of Additive Manufacturing on the market.
A main area of Additive Manufacturing is 3D printing of metal. In 3D printing, a laser melts fine-grained metal powder at selected, exactly defined locations. The components rebuilt up layer upon layer: A wafer-thin layer of metal powder is spread out on a powder bed. Then the laser melts the powder at the programmed spots. When this has been completed, another thin layer of powder is applied, and so forth... With this technique it is possible to make components of a complexity not feasible with conventional techniques. SMS group has been very active in the field of Additive Manufacturing for many years and has recently commissioned a pilot plant for industrial-scale production of AM-grade metal powder. This powder features very specific properties, which are very likely to propel a completely new growth sector. It is extremely homogeneous and forms the basis of Additive Manufacturing. The powder consists of perfectly round minute spheres measuring only 15 to 45 micrometers (one thousandth of a millimeter). It is hard to imagine how these microscopic particles are produced in a 13 meters tall and complex high-tech plant. Markus Hüllen, Vice President 3D Competence Center of SMS group: “The successful commissioning of the powder atomization plant marks a milestone for SMS group because it ensures the quality we need to make high-quality 3D-printed metal components. Our objective is to master – and allow our customers to master - the complete process chain of this innovative technology. This is why we deliberately chose to not build a small-scale but an industrial-scale pilot plant. Only this way can we test the process under realistic conditions, i.e. at high temperatures and pressures and in long production campaigns. We also work with a cooperation partner: Additive Industries, developers and providers of selective laser melting systems for 3D metal powder printing. We plan to set up a demonstration plant at the SMS group facilities in Mönchengladbach, which will comprise all process steps of Additive Manufacturing. “
Additively manufactured components are already used in a number of industries. These “enabler” industries include the aerospace industry, the automotive industry, medical engineering, prototype and tool making, and plant and mechanical engineering. The Demo Center at the Mönchengladbach facilities will be the first of its kind as it will allow customers to experience the complete process chain of Additive Manufacturing, i.e. from powder production in the powder atomization plant, powder handling, 3D printing, heat treatment and machining to inspection, quality checks, logistics and the automation system. SMS group has been cooperating with Additive Industries in the development of processes that keep the powder under vacuum during all process steps. This prevents the powder from contaminating in any way and ensures that the components produced will be of highest quality. Markus Hüllen: “As systems provider and the “Leading Partner in the World of Metals”, our objective is to offer our customers complete Additive Manufacturing plants on a turnkey basis. By integrating the entire process chain from powder production down to the finished products, we ensure a high and reproducible powder quality for series production. The pilot plant will allow us to optimize the processes so as to maximize productivity and minimize total costs. Our customers will receive modular, scalable solutions tailored to their individual requirements. With our world-spanning service and support network, we are always readily available for our customers to accompany them on their way into the world of Additive Manufacturing.“
Although the new spraying system for drop forging plants is only a small object, it is – in the true sense of the word – a prize example of the exciting developments the plant and mechanical engineering sector is going to see in the very near future. With its corporate-wide strategy program “New Horizon”, SMS group is bundling all future-oriented activities in connection with Additive Manufacturing, digitalization, Industrie 4.0 and new high-tech materials. The reason behind this strategy is the fact that all these areas are interconnected and can only be advanced in a concerted approach. The strategy has worked out well. Numerous projects, such as learning steel mills, plants for the production of high-performance materials, and environmental technology that provides both ecological and economic benefits have already been successfully implemented. The new 3D-printed spray heads certainly fits into this category.