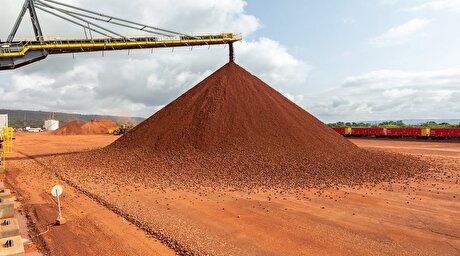
Industry 4.0, Foundry 4.0, Guss 4.0 - nowadays developments are occurring so fast that instead of new concepts, only version designations are being assigned. With its vision of Guss 4.0, Christenguss AG of Bergdietikon in Switzerland is also blazing the trail into a digital future.
The constant pursuit of modernization and optimization mean that Christenguss is already presenting itself as a top modern foundry that manufactures complex sand casting molds in a 3D printing process. It is in this way that the Bavarian company ExOne from Gersthofen near Augsburg provides a valuable service with an S-Max production printer. This allows the foundry the production of sand molds of the highest quality and great individuality, from batch sizes upwards.
"Obsolete parts can thus be quickly reproduced in reverse engineering by means of the digital process," confirms Holger Barth of ExOne. "For example, if the original manufacturer is no longer in business or no longer offering the part." He also makes the point that Christenguss has become a real specialist in the field of tool-less mold production – particularly by using the S-Max-printer: "It produces complex sand cores and molds directly from CAD data, eliminating the need for physical models. In this way, Christenguss even produces complex inner contours with a printed sand core from the S-Max."
Changes and optimizations in the CAD data can be implemented immediately in the product design and the casting can therefore start within a short time and without additional tools. There is also a great freedom of design when printing detailed, high-precision cores and complex geometries.
In conclusion, Florian Christen again refers to time and cost savings: "Thanks to the 3D-printing of the molds, positioning systems can also be integrated directly into the sprue for a casting. As a result, this means specific set-ups for machining and plastering of parts are only necessary to a very limited extent."
This is another benefit for the foundry and thus also for their customers – and a wonderful prospect for Florian Christen's vision of Guss 4.0.