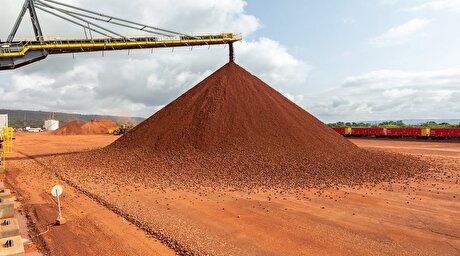
With SMS group’s TMbaR process, it is possible to produce fine-grained final products while reducing the content of expensive alloys in the input stock.
Both TMbaR mills will be equipped with a HSD® (High-Speed Delivery) system.
Thermomechanical rolling is a forming process in which final reduction is carried out within a defined temperature range leading to specific properties of the rolled stock. Thus, sufficient capacity for cooling and equalization has to be provided for in the plant design. The lower rolling temperatures (750 to 820 degrees Celsius) require higher rolling forces and consequently wire rod blocks capable of sustaining very high loads. Under these rolling conditions, grain sizes that in conventional rolling would typically range between ASTM 8 and 10 can be improved to ASTM 12 with thermomechanical rolling. Key components of the SMS group TMbaR technology are a loop line with water boxes for controlled cooling and equalizing and a MEERdrive® finishing block. Besides its rigid design, which allows rolling forces so far unattained in the market, the MEERdrive® block is equipped with a single drive which provides the flexibility required to optimally control recrystallization after rolling.
Two companies have now decided in favor of the TMbaR technology: Lianxin Steel and Shandong Laigang Yongfeng.
Lianxin Steel has ordered a TMbaR mill for its Dafeng site. The plant will be designed for an annual production of 1,000,000 tons of rebar with diameters ranging between 8 and 40 millimeters at a maximum rolling speed of 45 meters per second. SMS group will supply all rolling mill stands for the roughing, intermediate and finishing mills, including two six-stand MEERdrive® finishing blocks, shears, water boxes as well as the double HSD® system. Additionally, the complete package of electrical and automation systems as well as supervision of erection and commissioning are in the scope of supply. The plant is scheduled to be started up by the end of 2018.
The TMbaR mill for Shandong Laigang Yongfeng´s Dezhou site is part of a capacity conversion program using the EAF-based production route to replace the existing facilities. The new plant will be designed for an annual production of 1,000,000 tons of rebar in diameters ranging between 8 and 32 millimeters. This includes straight bars with diameters between 8 and 25 millimeters to be rolled at a maximum speed of 45 meters per second and bar-in-coil in diameters ranging from 8 to 32 millimeters to be rolled at a maximum speed of 35 meters per second. Yongfeng is going to install two five-strand continuous casting machines supplied by SMS Concast as well as a new high-speed rolling area, including two six-stand MEERdrive® finishing blocks, cooling and equalizing lines, a high-speed outlet consisting of a two-strand HSD® (High-Speed Delivery) system with dividing shears and pinch roll unit as well as a VCC® (Vertical Compact Coiler) system for coils weighing up to five tons. Additionally, the electrical and automation systems for the three mechanical packages and supervision of erection and commissioning will be supplied. The plant is scheduled to start production in 2019.
Both companies put their trust in the long-standing experience of SMS group and its one-step-ahead TMbaR technology, which will allow Lianxin Steel and Shandong Laigang Yongfeng to respond better and faster to market demands, achieve improved material properties and save on alloys and operating costs.
Yongfeng´s TMbaR mill will additionally be equipped with a VCC® (Vertical Compact Coiler) system.