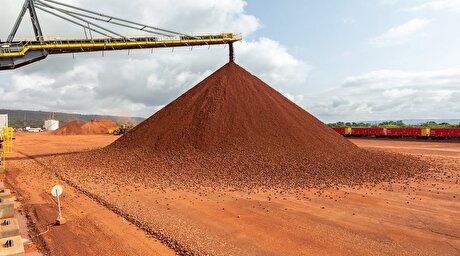
“I am very enthusiastic about the innovations we have brought into the digital world in recent years,” Antonello Mordeglia, President & CEO of Danieli Automation said during the welcome speech introducing new technologies for energy-savings, robotics, automation and Big Data”.
In order of presentation:
“Advanced human-machine interaction: implementing virtual reality and mobile solutions,” examined the possibilities that the current age of new technologies provides multiple independent users with new access to extensive volumes of data and resources.
Real-time data, real-time decisions, real-time actions – but most important, real-time results, smart phone and tablets are the new way to access information. The presentation described the numerous examples of individual communication devices functioning reliably as control devices for effective, immediate, and safe steel plant operations.
“Danieli and robotics: the robotic-human experience,” portrayed a range of robotics for effective operating capabilities while ensuring the safety of people, the protection of the environment, and the quality and capability of the results.
Danieli Telerobot Labs presented how from the meltshop to the finishing area, the Q-Melt, Q-Cast, Q-Roll, and Q-Zinc tech packages take advantage of automation programming and robotic devices to support productive operations.
“Dedicated Instrumentation for Metals Industry” described how multiple Danieli technology packages are applied to expand the scope of performance control and provide an easy-to-install point of continuity with Industry 4.0 include Hi-POWDER, Intelligrind, Q-VID ODL, SM 3100, HiSECTION, HiWIDTH, HiTHIX, and Q-VID Spool, among others.
“Manufacturing Execution & Optimization: a unique contribution to plant digitalization,” began by introducing the concept of Manufacturing Execution Systems (MES), which may be seen as an intermediate step between ERP and process control. Collecting and using information for a business process is a daily challenge, and Danieli Automation with its MES shifts the focus from execution to optimization of the processes.
First, the Q3-MET package provides the link between ERP and process control systems, operating as a Master Data module through individual platforms for Order Management, Planning and Scheduling, etc. The Q3-MET digital architecture supports all metallurgical processes, while functional organization reduces the systems involves, which has positive effects on maintenance and Total Cost of Ownership.
“Q-Drive and Q-Heat: large drives and induction heating systems for metals”, emphasized how the growing demand for industrial savings and modernization of industrial plants is increasing the value of induction heating technology. Danieli Automation Q-Drive and Q-Heat packages are large drives and induction heating technologies designed to cover every medium- and high-voltage application for metals production. Both Q-Drive and Q-Heat fulfill the value proposition of induction heating with remote connectivity, advanced diagnostics, and modular design.
“Data-Driven Technologies: Applying predictive analytics to extract knowledge for process optimization” examined the vast potential for drawing more useful and applicable knowledge from data that already is collected in metal producing operations. A modern data-driven approach requires an effective organization and business model to work properly, including integrated data acquisition, analysis and a problem-solving platform. Danieli Q3Intelligence is such a platform, and dedicated to metals industry operations.
“Teleservice assistance, smart helmets and remote commissioning” revealed the potential for smart phones and tablets to control process functions effectively in steelmaking. Danieli Automation’s Customer Service department works to extend such resources, functions, and assistance to customers around the world. It provides technical assistance for automation systems, electrical parts for steelmaking plants, and equipment.
This assistance includes the Smart Helmet device, which introduces a virtual reality function to the remote assistance, allowing the technician to view and interact with the situation at the remote plant site or other location.
“Pursuing ‘zero accidents’ target: how digitalization can improve safety in the metals industry,” addressed the potential for automation technologies to support workers’ safety. An accident-free working environment is possible by adopting an “active” workplace safety plan – avoiding accidents - in contrast to a “passive” approach - which seeks simply to reduce the effects of accidents.
Furthermore, Fourth Danieli Innovaction Meeting gave guests the possibility to visit some technologically advanced plants for the production of flat and long product plants, which in respective sectors are benchmarks.
Tata Steel, Ijmuiden, The Nederlands: Integrated Steel Plant for Flat Products;
Acciaieria Arvedi, Cremona, Italy: Cold Strip Mill Complex;
Marcegaglia, Ravenna, Italy: Cold Strip Mill Complex;
Voestalpine, Donawitz, Austria: Wire Rod and Bar-in-Coil Mill;
Ferriere Nord, Osoppo, Italy: Wire Rod and Bar Mill;
ABS, Cargnacco, Italy: Minimill for SBQ Products.